Das Biegen ist eine der häufigsten Blechbearbeitungsarten. Dieses Verfahren, das auch als Pressbiegen, Bördeln, Gesenkbiegen, Falten und Kanten bekannt ist, wird verwendet, um ein Material in eine winklige Form zu verformen.
Dies geschieht durch die Anwendung von Kraft auf ein Werkstück. Die Kraft muss die Streckgrenze des Materials überschreiten, um eine plastische Verformung zu erreichen. Nur dann erhält man ein dauerhaftes Ergebnis in Form einer Biegung.
Welches sind die gängigsten Biegeverfahren? Wie wirkt sich die Rückfederung auf die Biegung aus? Was ist der k-Faktor? Wie berechnet man die Biegezugabe?
Alle diese Fragen werden in diesem Beitrag zusammen mit einigen Tipps zum Biegen erörtert.
Wir haben auch einen weiteren wichtigen Beitrag über Abkantwerkzeuge geschrieben. Die Kenntnis der Werkzeuge hilft dir, Produkte zu entwickeln, die hergestellt werden können.
- Biegemethoden
- V-Biegen
- Bodenpressen
- Luftbiegen
- Prägen
- U-Biegen
- U-Biegematrize mit hydraulischer Presse -U-Bükme Kalıbı
- Stufenbiegen
- Stufenbiegen mit Bystronic Abkantpresse vollautomatisch
- Walzenbiegen
- W11 mechanische 3-Walzen-Symmetrische Blechwalzmaschine
- Wischbiegen
- Rotationsbiegen
- Rolla-V-Biegen
- Rückfederung beim Biegen
- Biegetoleranz und K-Faktor
- Berechnung der Biegezugabe
- Blechdesign-Tipps zum Biegen
- Mindestflanschlänge
- Fasen an den Seiten
- Lochabstand von der Biegung
- Symmetrie
- Nietmuttern
- Kleine Flansche an großen Teilen
- Bögen nebeneinander
- Keep the Bends on the Same Line
- Die Biegelinie ist parallel zu einer Seite
- Biegeentlastung
- Biegen eines Kastens
- Prüfen Sie das flache Muster
- Faustformel für den Mindestbiegeradius
- Biegerichtungen
- Säumen
- Betrachten Sie das Material
- Metal Bending Online
Biegemethoden
Es gibt eine ganze Reihe verschiedener Biegemethoden. Jede hat ihre eigenen Vorteile. Das Dilemma besteht meist darin, ob man sich für Genauigkeit oder Einfachheit entscheidet, wobei letzteres häufiger verwendet wird. Einfachere Methoden sind flexibler und benötigen vor allem weniger verschiedene Werkzeuge, um ein Ergebnis zu erzielen.
V-Biegen
V-Biegen ist die gebräuchlichste Biegemethode mit Stempel und Matrize. Es hat drei Untergruppen: das Gesenkbiegen, das Luftbiegen und das Prägen. Luftbiegen und Prägen machen etwa 90 % aller Biegearbeiten aus.
Die nachstehende Tabelle hilft Ihnen, die Mindestflanschlänge b (mm) und die Innenradien ir (mm) in Abhängigkeit von der Materialstärke t (mm) zu ermitteln. Sie können auch die Matrizenbreite V (mm) sehen, die für diese Spezifikationen erforderlich ist. Für jeden Arbeitsgang ist eine bestimmte Tonnage pro Meter erforderlich. Diese ist ebenfalls in der Tabelle angegeben. Sie können sehen, dass dickere Materialien und kleinere Innenradien mehr Kraft bzw. Tonnage erfordern. Die hervorgehobenen Optionen sind empfohlene Spezifikationen für das Metallbiegen.
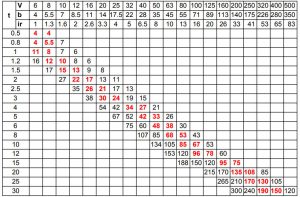
Angenommen, ich habe ein 2 mm dickes Blech und möchte es biegen. Der Einfachheit halber verwende ich auch einen Innenradius von 2 mm. Ich sehe jetzt, dass die Mindestflanschlänge für eine solche Biegung 8,5 mm beträgt, also muss ich dies bei der Konstruktion berücksichtigen. Die erforderliche Matrizenbreite ist 12 mm und die Tonnage pro Meter beträgt 22. Die niedrigste übliche Bankkapazität liegt bei 100 Tonnen. Die Biegelinie meines Werkstücks ist 3 m lang, also beträgt die erforderliche Gesamtkraft 3*22=66 Tonnen. Daher reicht auch eine einfache Werkbank mit genügend Platz zum Biegen von 3 m langen Stücken aus.
Eine Sache muss jedoch beachtet werden. Diese Tabelle gilt für Konstruktionsstähle mit einer Streckgrenze von etwa 400 MPa. Wenn Sie Aluminium biegen wollen, können Sie den Tonnagewert durch 2 teilen, da es weniger Kraft benötigt. Bei rostfreiem Stahl ist das Gegenteil der Fall – die benötigte Kraft ist 1,7-mal höher als die in dieser Tabelle angegebene.
Bodenpressen
Bodenpressen wird auch als Bodenpressen oder Bodenschlagen bezeichnet. Wie der Name „Bodenpressen“ schon sagt, drückt der Stempel das Blech auf die Oberfläche der Matrize, so dass der Winkel der Matrize den endgültigen Winkel des Werkstücks bestimmt. Beim Bodenpressen hängt der innere Radius des abgewinkelten Blechs vom Radius der Matrize ab.
Wenn die innere Linie zusammengedrückt wird, braucht sie immer mehr Kraft, um sie weiter zu bearbeiten. Das Absenken ermöglicht es, diese Kraft auszuüben, da der endgültige Winkel voreingestellt ist. Die Möglichkeit, mehr Kraft aufzubringen, verringert den Rückfederungseffekt und sorgt für eine gute Präzision.
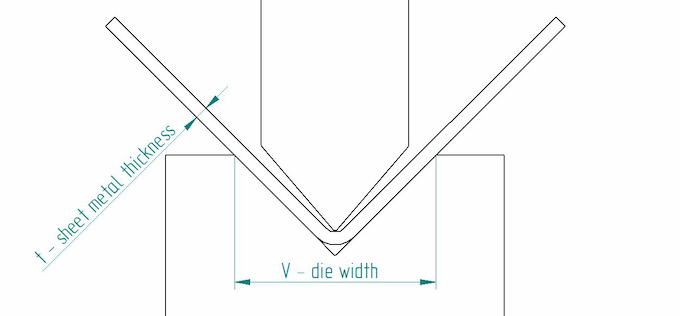
Beim Bottoming ist ein wichtiger Schritt die Berechnung der V-Matrizenöffnung.
Öffnungsbreite V (mm) | ||||
Methode/Dicke (mm) | 0.5…2.6 | 2.7…8 | 8.1…10 | Über 10 |
Bottoming | 6t | 8t | 10t | 12t |
Luftbiegen | 12…15t | |||
Biegen | 5t |
Der innere Radius ist experimentell nachgewiesen etwa 1/6 der Öffnungsbreite, d.h. die Gleichung sieht wie folgt aus: ir=V/6.
Luftbiegen
Das Teilbiegen oder Luftbiegen verdankt seinen Namen der Tatsache, dass das Werkstück die Werkzeugteile nicht vollständig berührt. Beim Teilbiegen ruht das Werkstück auf 2 Punkten und der Stempel drückt die Biegung. Es wird immer noch normalerweise mit einer Abkantpresse durchgeführt, aber es gibt keine Notwendigkeit für eine seitliche Matrize.
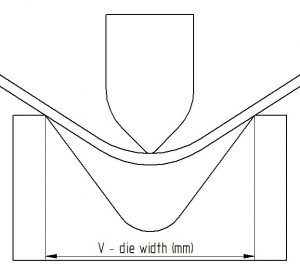
Das Luftbiegen bietet viel Flexibilität. Nehmen wir an, Sie haben eine 90°-Matrize und einen Stempel. Mit dieser Methode können Sie ein Ergebnis zwischen 90 und 180 Grad erzielen. Auch wenn es weniger genau ist als das Tiefziehen oder Prägen, ist diese Einfachheit das Schöne an dieser Methode. Wenn die Last losgelassen wird und die Rückfederung des Materials zu einem falschen Winkel führt, lässt sich das leicht korrigieren, indem einfach etwas mehr Druck ausgeübt wird.
Natürlich ist dies eine Folge der geringeren Genauigkeit im Vergleich zum Tiefziehen. Der große Vorteil des partiellen Biegens ist jedoch, dass bei unterschiedlichen Biegewinkeln kein Umrüsten erforderlich ist.
Erhalten Sie Ihr Angebot für die Metallverarbeitung in Sekunden
-
Angebot in Sekunden
-
Kurze Lieferzeiten
-
Lieferung per Fraktur
Angebot einholen
Prägen
Prägen war früher viel weiter verbreitet. Es war so ziemlich die einzige Möglichkeit, genaue Ergebnisse zu erzielen. Heute sind die Maschinen so gut kontrollierbar und präzise, dass solche Methoden nicht mehr weit verbreitet sind.
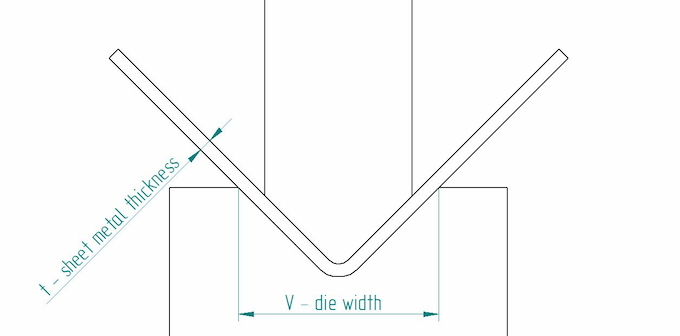
Das Prägen hat seinen Namen von den Münzen, denn sie müssen identisch sein, damit Falschgeld von echtem Geld unterschieden werden kann. Die Münzprägung beim Biegen liefert ähnlich präzise Ergebnisse. Wenn Sie beispielsweise einen 45-Grad-Winkel erzielen wollen, benötigen Sie einen Stempel und eine Matrize mit genau demselben Winkel. Es gibt keine Rückfederung zu befürchten.
Warum? Weil die Matrize in das Blech eindringt und eine Delle in das Werkstück drückt. Dies und die hohen Kräfte (etwa 5-8 mal so hoch wie beim Teilbiegen) garantieren eine hohe Präzision. Die eindringende Wirkung sorgt auch für einen sehr kleinen Innenradius der Biegung.
U-Biegen
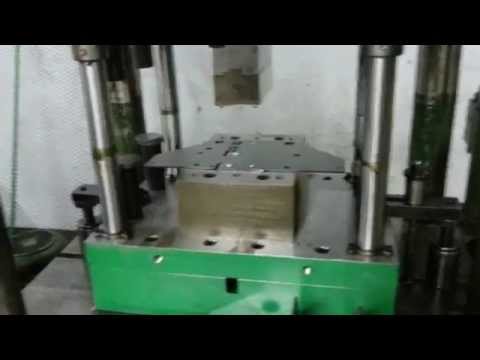
U-Biegematrize mit hydraulischer Presse -U-Bükme Kalıbı
U-Biegen ist im Prinzip dem V-Biegen sehr ähnlich. Es gibt eine Matrize und einen Stempel, dieses Mal sind beide U-förmig, was zu einer ähnlichen Biegung führt. Dies ist eine sehr einfache Methode, um z. B. U-Profile aus Stahl zu biegen, aber nicht so häufig, da solche Profile auch mit anderen, flexibleren Methoden hergestellt werden können.
Stufenbiegen
Stufenbiegen ist im Wesentlichen ein sich wiederholendes V-Biegen. Diese Methode, die auch als Buckelbiegen bezeichnet wird, verwendet viele aufeinanderfolgende V-Biegungen, um einen großen Radius für das Werkstück zu erhalten. Die endgültige Qualität hängt von der Anzahl der Biegungen und den Abständen zwischen ihnen ab. Je mehr, desto glatter das Ergebnis.
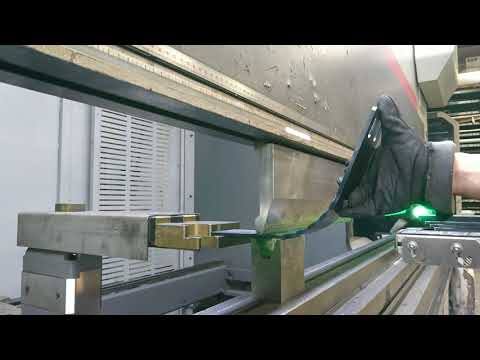
Stufenbiegen mit Bystronic Abkantpresse vollautomatisch
Das Buckelbiegen wird in vielen Fällen eingesetzt. Einige Beispiele sind konische Trichter und Schneepflüge. Es ermöglicht das Biegen von großen Radien mit normalen Werkzeugen. Das einfachere Einrichten macht es preiswerter, besonders bei kleinen Serien.
Walzenbiegen
Walzenbiegen wird zur Herstellung von Rohren oder Kegeln in verschiedenen Formen verwendet. Es kann bei Bedarf auch für die Herstellung von Biegungen mit großem Radius verwendet werden. Je nach Kapazität der Maschine und Anzahl der Walzen können eine oder mehrere Biegungen gleichzeitig durchgeführt werden.
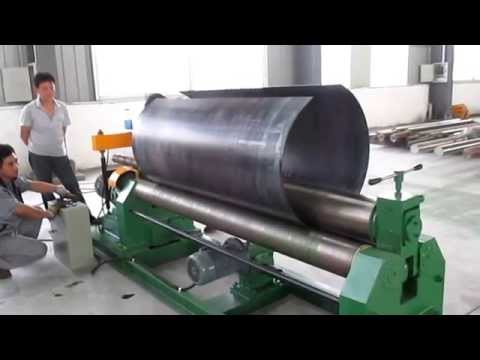
W11 mechanische 3-Walzen-Symmetrische Blechwalzmaschine
Dabei gibt es zwei Antriebswalzen und eine dritte einstellbare Walze. Diese bewegt sich über Reibungskräfte mit. Soll das Teil sowohl an den Enden als auch in der Mitte gebogen werden, ist ein zusätzlicher Arbeitsgang erforderlich. Dies geschieht mit einer hydraulischen Presse oder Abkantpresse. Andernfalls werden die Kanten des Teils flach.
Wischbiegen
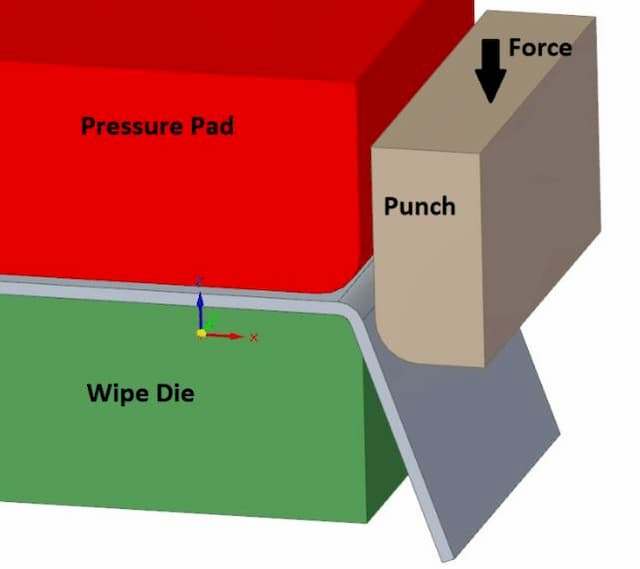
Wischbiegen, oder Kantenbiegen, ist eine weitere Möglichkeit, Blechkanten zu biegen. Dabei ist es wichtig, dass das Blech richtig auf die Matrize geschoben wird. Daher bestimmt die Matrize auch den Innenradius der Biegung. Das Spiel zwischen der Matrize und dem Stempel spielt eine wichtige Rolle, um ein gutes Ergebnis zu erzielen.
Rotationsbiegen
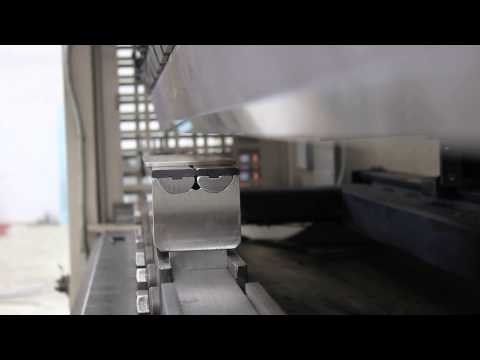
Rolla-V-Biegen
Eine weitere Möglichkeit zum Biegen von Kanten ist das Rotationsbiegen. Es hat einen großen Vorteil gegenüber dem Wischbiegen oder V-Biegen – es zerkratzt nicht die Oberfläche des Materials. Es gibt sogar spezielle Polymer-Werkzeuge, die jede Art von Werkzeugmarkierung, geschweige denn Kratzer vermeiden. Rotationsbieger können auch schärfere Ecken als 90 Grad biegen. Dies ist bei den üblichen Winkeln sehr hilfreich, da die Rückfederung kein Problem mehr darstellt.
Die gängigste Methode ist die mit zwei Rollen, aber es gibt auch Optionen mit einer Rolle. Diese Methode eignet sich auch für die Herstellung von U-Profilen mit nahe beieinander liegenden Flanschen, da sie flexibler ist als andere Methoden.
Wenn Sie auch über Stahlrohrbiegemethoden lesen möchten, finden Sie diese zusammen mit Rohrbiegemaschinen.
Rückfederung beim Biegen
Beim Biegen eines Werkstücks federt dieses nach dem Anheben der Last naturgemäß ein wenig zurück. Deshalb muss dies beim Biegen kompensiert werden. Das Werkstück wird über den gewünschten Winkel hinaus gebogen, so dass es nach der Rückfederung die gewünschte Form annimmt.
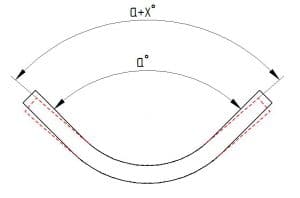
Ein weiterer Punkt, den es zu beachten gilt, ist der Biegeradius. Je größer der Innenradius ist, desto größer ist der Rückfederungseffekt. Ein scharfer Stempel ergibt einen kleinen Radius und entlastet die Rückfederung.
Warum tritt die Rückfederung auf? Beim Biegen von Teilen wird die Biegung in zwei Schichten unterteilt, die durch eine Linie – die neutrale Linie – voneinander getrennt sind. Auf jeder Seite findet ein anderer physikalischer Prozess statt. Auf der „Innenseite“ wird das Material zusammengedrückt, auf der „Außenseite“ wird es gezogen. Jede Metallart hat unterschiedliche Werte für die Belastungen, die sie beim Zusammendrücken oder Ziehen aufnehmen kann. Und die Druckfestigkeit eines Materials ist der Zugfestigkeit weit überlegen.
Daher ist es schwieriger, auf der Innenseite eine dauerhafte Verformung zu erreichen. Das bedeutet, dass die komprimierte Schicht nicht dauerhaft verformt wird und versucht, nach dem Aufheben der Last wieder ihre frühere Form anzunehmen.
Biegetoleranz und K-Faktor
Wenn Sie Ihre gebogenen Blechteile in einer CAD-Software entwerfen, die über eine spezielle Blechumgebung verfügt, verwenden Sie diese. Es gibt sie aus gutem Grund. Bei der Herstellung von Biegungen werden die Materialspezifikationen berücksichtigt. All diese Informationen sind notwendig, wenn Sie ein flaches Muster für das Laserschneiden anfertigen.
Wenn Sie nicht unseren Fertigungsservice nutzen, bei dem CAD-Modelle für die Produktion akzeptiert werden, müssen Sie weiterhin diese flachen Musterzeichnungen anfertigen.
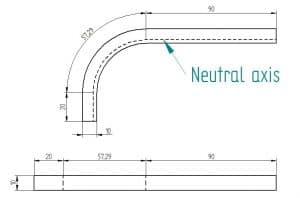
Wenn Sie Ihre flachen Musterzeichnungen selbst anfertigen, müssen Sie Folgendes wissen. Durch das Biegen wird das Material gedehnt. Das bedeutet, dass die neutrale Linie oder Achse, wie im Abschnitt über die Rückfederung beschrieben, nicht wirklich in der Mitte des Materials liegt. Aber das flache Muster muss entsprechend der neutralen Linie geformt werden. Und um ihre Position zu finden, braucht man den k-Faktor.
Der k-Faktor ist eine empirische Konstante, d.h. sein Wert wurde durch Tests ermittelt. Er variiert je nach Material, dessen Dicke, Biegeradius und Biegemethode. Im Grunde genommen versetzt der k-Faktor die neutrale Linie, um ein flaches Muster zu erhalten, das der Realität entspricht. Wenn man ihn verwendet, erhält man die Biegezugabe, die im Wesentlichen die Länge der gekrümmten neutralen Achse ist.
K-Faktor-Formel:
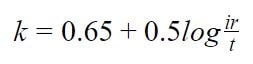
k – k-Faktor, konstant; ir – Innenradius (mm); t – Blechdicke (mm)
Biegezugabe-Formeln:
Für Biegungen zwischen 0 und 90 Grad lautet die Formel wie folgt:

ß – Biegewinkel (°)
Für Biegungen zwischen 90 und 165 Grad lautet die Formel:

Für Biegungen über 165° ist es nicht notwendig, Biegezugaben zu berechnen, da die neutrale Achse ziemlich genau in der Mitte des Details liegt.
Berechnung der Biegezugabe
Angenommen, Sie haben ein ähnliches Teil wie das auf dem Bild oben – es hat einen geraden Schenkel von 20 mm und einen weiteren von 70 mm. Der Biegewinkel beträgt 90°, die Blechdicke 5 mm und der Innenradius 6 mm. Wir wollen die endgültige Länge des Teils wissen. Zuerst müssen wir mit dem k-Faktor beginnen:

Eine andere Möglichkeit, den k-Faktor zu bestimmen, ist die „Faustregel“. Wählen Sie einfach einen k-Faktor für Ihr Material aus der nachstehenden Tabelle aus. Dies führt in den meisten Fällen zu ausreichend genauen Ergebnissen.
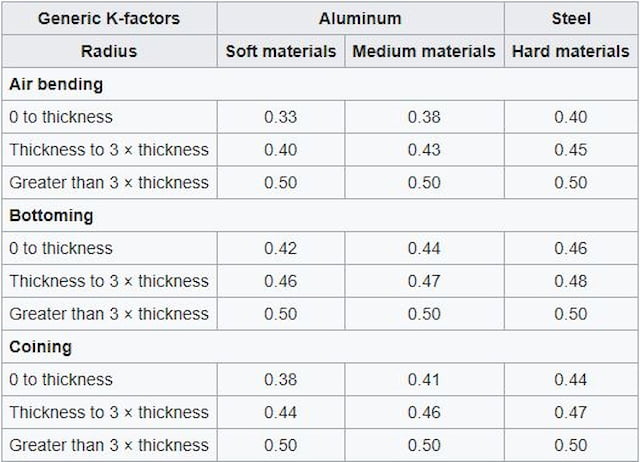
Nun können wir zur Biegezugabe übergehen:

Für die endgültige Länge addieren wir einfach die beiden Schenkellängen zur Biegezugabe:

Blechdesign-Tipps zum Biegen
So sprach ich mit unserem erfahrenen Vertriebsingenieur, der sich mit dem Biegen von Blechen auskennt. Er war Feuer und Flamme und beschloss, die Gelegenheit zu nutzen, um seine Erkenntnisse über das Blechbiegen weiterzugeben. So brachte er eine Liste mit häufigen Fehlern und Lösungen, um sie zu vermeiden.
Mindestflanschlänge
Wie bereits erwähnt, gibt es eine Mindestflanschlänge. Als Orientierung dient die Biegekrafttabelle. Je nach Dicke wird die Matrizenbreite ausgewählt. Wenn Sie einen Flansch entwerfen, der zu kurz ist, wird er ungünstig in den Spalt „fallen“ und Sie werden nicht das gewünschte Ergebnis erhalten.
Fasen an den Seiten
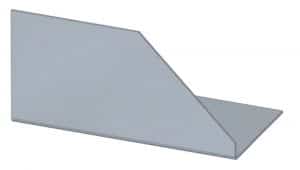
Wenn Sie einen Flansch herstellen wollen, der an einem oder zwei Enden gefast ist, gilt immer noch die vorhergehende Regel einer Mindestflanschlänge. Die Fasen müssen genug Platz lassen, um richtige Biegungen zu erreichen, sonst sieht es nur verformt aus und niemand ist wirklich zufrieden.
Lochabstand von der Biegung
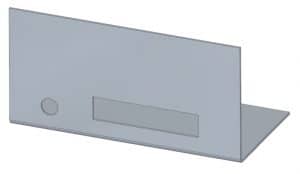
Wenn die Löcher zu nahe an der Biegung sind, können sie verformt werden. Runde Löcher sind nicht so problematisch wie andere Typen, aber Ihre Schrauben passen möglicherweise trotzdem nicht durch. Auch hier sollten Sie die Mindestmaße für den Flansch aus der Biegekrafttabelle entnehmen und die Löcher weiter als das Minimum setzen.
Symmetrie
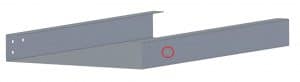
Eine große Gefahr liegt darin, Teile herzustellen, die fast symmetrisch sind. Wenn möglich, machen Sie es symmetrisch. Wenn es fast symmetrisch ist, kann der Bediener der Biegepresse verwirrt werden. Das Ergebnis? Ihr Teil wird in die falsche Richtung gebogen.
Die Symmetrie kann nicht in jedem Fall garantiert werden, aber stellen Sie sicher, dass es leicht verständlich ist, wie die Herstellung erfolgen soll.
Nietmuttern
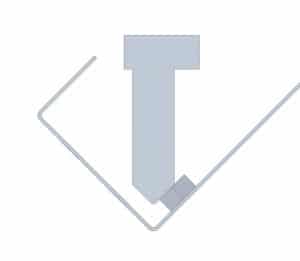
Wenn Sie Nietmuttern in der Nähe der Biegelinie verwenden, ist es bekannt, dass es gut ist, sie vor dem Biegen einzusetzen, um die Anwendbarkeit zu sichern. Nach dem Biegen können die Löcher deformiert werden. Achten Sie jedoch darauf, dass die Muttern beim Biegen nicht im Weg sind.
Kleine Flansche an großen Teilen
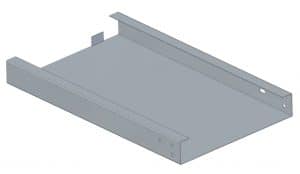
Bei großen und schweren Teilen ist es besser, kleine Flansche wegzulassen. Das macht die Herstellung sehr schwierig, und es kann Handarbeit erforderlich sein. Aber es kostet mehr als eine einfache Bearbeitung. Daher ist es klüger, sich für eine alternative Lösung zu entscheiden, wenn dies möglich ist.
Bögen nebeneinander
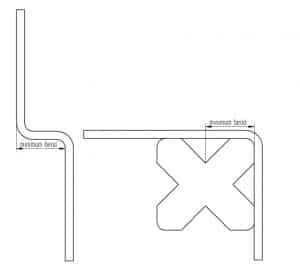
Wenn Sie aufeinanderfolgende Biegungen einbeziehen wollen, prüfen Sie, ob dies machbar ist. Ein Problem tritt auf, wenn Sie das bereits gebogene Teil nicht in die Matrize einpassen können. Wenn Ihre Biegungen in die gleiche Richtung zeigen – eine U-Biegung -, dann ist eine gängige Regel, das Zwischenteil länger als die Flansche zu gestalten.
Keep the Bends on the Same Line
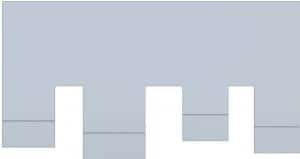
Es ist am besten, die Biegungen auf der gleichen Linie zu halten, wenn Sie mehrere Flansche hintereinander haben. Auf diese Weise können Sie die Anzahl der Arbeitsgänge auf ein Minimum reduzieren. Andernfalls muss der Bediener die Teile für jede einzelne Biegung neu einstellen, was mehr Zeit und mehr Geld bedeutet.
Die Biegelinie ist parallel zu einer Seite
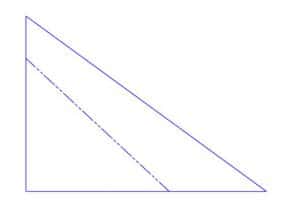
Wie die Überschrift schon sagt. Es muss eine parallele Seite zu Ihrer Biegelinie vorhanden sein, um sie zu positionieren. Ist dies nicht der Fall, bereitet das Ausrichten des Teils Kopfzerbrechen, und Sie erhalten möglicherweise ein unbefriedigendes Ergebnis.
Biegeentlastung
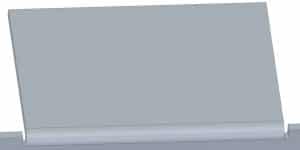
Um ein optimales Ergebnis zu erzielen, ist es ratsam, nicht nur einen kleinen Laserschnitt, sondern einen echten Ausschnitt an den Seiten des zu biegenden Flansches vorzunehmen – eine Biegeentlastung. Die Breite eines solchen Schnitts sollte über der Materialdicke liegen. Dadurch wird sichergestellt, dass es bei der endgültigen Biegung keine Risse oder Verformungen gibt. Eine weitere gute Praxis ist es, kleine Radien in die Biegeaussparungen einzubauen, da sie auch Materialspannungen abbauen.
Biegen eines Kastens
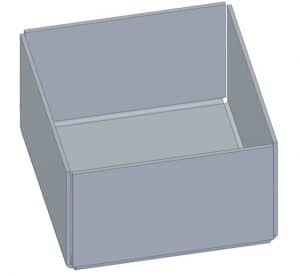
Beim Biegen eines Kastens sollten kleine Lücken zwischen den Flanschen gelassen werden. Andernfalls kann die letzte Biegung in die bereits vorhandenen krachen und die ganze Struktur brechen.
Prüfen Sie das flache Muster
Eine Sache, die Sie im Auge behalten sollten, ist das Umschalten Ihrer CAD-Ansicht auf das flache Muster von Zeit zu Zeit. Das hat viele Vorteile. Erstens: Wenn Sie sich mit Ihren Flanschen verzetteln, kann es passieren, dass Sie mit etwas enden, das in einem flachen Muster nicht existieren kann. Was es in einem flachen Muster nicht geben kann, kann es auch auf keine andere Weise geben.
Messen Sie das Layout. Vielleicht können Sie den Entwurf so anpassen, dass er optimal passt. Versuchen Sie, ein größeres Blatt zu vermeiden, wenn die kleinere Größe in Reichweite ist. Vielleicht können Sie 2 Teile auf demselben Blatt unterbringen, wenn Sie nur ein paar Millimeter abnehmen? Das wird sich auf das endgültige Preisangebot auswirken.
Faustformel für den Mindestbiegeradius
Bewahren Sie die Einfachheit. Was könnte einfacher sein, als den Innenradius (ir) genauso zu wählen wie die Materialstärke. Das vermeidet spätere Probleme, Überlegungen und dumme Fehler. Ein Unterschreiten dieses Wertes kann Probleme mit sich bringen. Größere Radien erschweren nur einige andere Berechnungen.
Biegerichtungen

Sie sollten Ihre Biegungen nicht in der gleichen Richtung wie das Material gewalzt wurde konstruieren. Dies ist besonders wichtig bei Aluminium und Hardox. Natürlich kennen wir alle das Aluminiumgehäuse mit 4 Seiten, das Biegevorgänge im Gegensatz zu dem, was wir vorschlagen, bedeutet. Dennoch ist es besser, dies nach Möglichkeit zu vermeiden. Das Ergebnis können Unebenheiten oder sogar Risse sein.
Auch wenn die Fertigungsingenieure auf diese Dinge achten, ist es gut, sie selbst zu beachten. Es hilft, den Materialverbrauch zu berücksichtigen.
Säumen
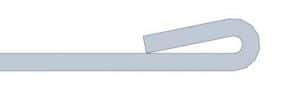
Wenn Sie die Kanten Ihres Blechs verstärken wollen, ist das Säumen eine gute Möglichkeit. Dennoch gelten einige Ratschläge. Es ist besser, einen kleinen Radius innerhalb des Saums zu lassen. Um den Radius vollständig zu zerdrücken, braucht man viel Kraft und Tonnage. Außerdem besteht dann die Gefahr, dass das Material reißt. Das Belassen eines Radius hingegen entschärft diese Gefahr.
Betrachten Sie das Material
Die normalen dünnen 1…3 mm Baustahlbleche können so ziemlich alles aushalten. Danach müssen Sie Ihre Forschung tun. Manche Materialien sind sehr viel kapriziöser im Umgang mit ihnen. Ein gutes Ergebnis hängt von Ihrem Wissen und der Hilfe Ihres Produktionsingenieurs ab.
Metal Bending Online
Fractory bietet die oben genannten Möglichkeiten auf einer webbasierten Plattform. Sie müssen nur Ihre STEP-Dateien auf unsere Plattform hochladen und wir werden Sie innerhalb von 24 Stunden mit dem endgültigen Angebot kontaktieren.
Selbstverständlich können Sie uns eine DXF-Zeichnung des flachen Musters zur Verfügung stellen, um einen automatischen Preis für das Schneideverfahren zu erhalten. Dies kann Ihnen bei der Optimierung des Designs und der Schätzung der Endkosten helfen.
Unsere Möglichkeiten:
Maximale Kraft: 1000 Tonnen
Maximale Länge der Biegelinie: 7200 mm
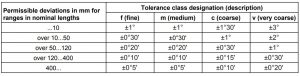
Wenn es keine zusätzlichen Anforderungen seitens des Kunden gibt, gelten die ISO-Standardtoleranzen für unsere Produkte. Die Biegetoleranzen sind in der obigen Tabelle aufgeführt.