Das Verständnis der 7 Verschwendungen ermöglicht es Ihnen, Prozessverschwendung zu erkennen, sei es in einem Produktions- oder Dienstleistungsunternehmen. Wenn man sie erkennt, kann man sie beseitigen und so die Effizienz, die Produktivität und den Gewinn steigern.
Ich halte dies für einen der wichtigsten Aspekte der schlanken Produktion. Wenn man sie sehen und fühlen kann, und noch wichtiger, wenn man sich in der Nähe von Verschwendung unwohl fühlt, dann hat man sie!
Das hat mein alter Mentor immer gesagt, und er hat Recht – wenn man „es“ versteht, bedeutet das, dass man „es“ versteht – und wenn man „es“ versteht, dann kann man es beseitigen!
Lassen Sie uns einen Blick darauf werfen, was die Abfälle sind, aber zuerst eine Definition.
NVA & VA
Die 7 Abfälle, von denen wir sprechen, beziehen sich auf Prozessabfälle. Die Japaner bezeichnen dies als Muda. Jede Aktivität, die in einem Unternehmen durchgeführt wird, ist entweder wertschöpfend (VA) oder nicht wertschöpfend (NVA).
Wertschöpfende Aktivitäten sind alle Aktivitäten, die ein Produkt oder eine Dienstleistung in den Augen des Kunden physisch verändern – Aktivitäten, die tatsächlich einen Mehrwert schaffen!
Non-Value-Add-Aktivitäten sind all jene Aktivitäten, die durchgeführt werden, die keinen Mehrwert schaffen. Einige davon mögen essentiell und notwendig sein, um die Arbeit zu erledigen, sind aber dennoch NVA, die die 7 Verschwendungen umfassen – Alle NVA-Kosten werden vom Unternehmen getragen.
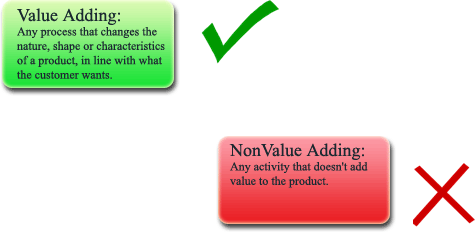
Ein Beispiel
Lassen Sie uns im Folgenden NVA und VA in einem einfachen Wertstrom betrachten.
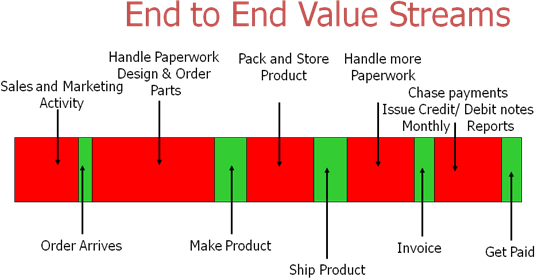
Das obige Diagramm zeigt NVA in rot und VA in grün.
Das Ziel ist es, so viel NVA wie möglich zu entfernen. Natürlich müssen einige Tätigkeiten erledigt werden, aber bei allen Aufgaben ist es wichtig, sich zu fragen, wie man diese „Muss-Aufgaben“ auf ein Minimum reduzieren kann.
Das ultimative Ziel ist es, alle NVA zu beseitigen (was nie erreicht werden wird, aber dennoch ein Ziel sein muss, um eine kontinuierliche Verbesserung zu erreichen). Jede Beseitigung oder Reduzierung von Verschwendung führt zu einer Verkürzung der Durchlaufzeiten:
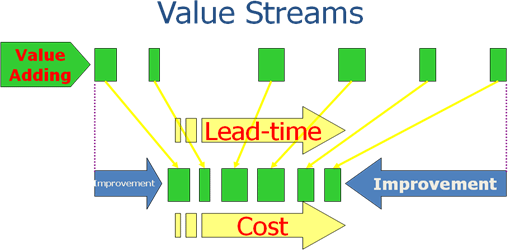
Die 7 Verschwendungen im Detail
Die 7 Verschwendungen sind nicht wertschöpfend und müssen als Feind gesehen werden. Sie absorbieren Zeit und Kosten.
Der Weg, sich an sie zu erinnern, ist, an Tim Wood zu denken. Dieser Typ ist in jedem Unternehmen zu finden, und es liegt in Ihrer Verantwortung, ihn aufzuspüren und so gut wie möglich zu reduzieren und zu eliminieren. Er absorbiert Kosten, Gemeinkosten und Bargeld im Unternehmen.
So, hier ist TIM WOOD!
T – Transport
I – Inventar
M – Bewegung
W – Warten und Verzögerungen
O – Überproduktion
O – Over Processing
D – Defects
Transport
Der Transport von Produkten und unfertigen Erzeugnissen ist notwendig, aber er muss in Bezug auf Zeit und Entfernung kontrolliert werden. Jedes Mal, wenn ein Produkt transportiert wird, besteht die Gefahr, dass es beschädigt wird, verloren geht, sich verzögert usw. Noch kritischer ist, dass je länger ein Produkt unterwegs ist, desto länger wird ihm kein Wert hinzugefügt, da es nicht physisch umgewandelt wird. Durch den Transport wird das Produkt, für das der Verbraucher bezahlen soll, nicht umgewandelt.
Bestände
Was produziert wird, um herumzusitzen und auf den nächsten Prozess zu warten, der nicht sofort beginnt, ist NVA. Das Produkt wartet und schafft keinen Mehrwert, wenn es irgendwo in einem Regal steht. Das Problem ist, dass es umso schlimmer ist, je mehr Vorräte vorhanden sind, denn diese können in Form von unfertigen Erzeugnissen, Rohmaterial oder Fertigwaren vorliegen.
Der springende Punkt ist, dass bei jeder dieser drei Formen von Vorräten, wenn sie nicht verkauft wurden, Bargeld in dem Material gebunden ist, das der Kunde noch nicht gekauft hat – dies führt zu einem massiven Abfluss von Barmitteln!
Bewegung
Ähnlich wie beim Transport, aber die Bewegung bezieht sich auf die Bewegung von Personal und Ausrüstung. Auch hier ist zu bedenken, dass es nicht wertschöpfend sein kann, wenn das Personal herumläuft und Dinge sucht und findet. Das Gleiche gilt für die Ausrüstung – wenn man Zeit damit verbringt, die Ausrüstung herumzuschleppen, kann man sie nicht zur Wertschöpfung und zum Geldverdienen einsetzen, und außerdem steigt die Gefahr von Schäden.
Warten und Verzögerungen
Wenn laufende Arbeiten und Waren nicht bearbeitet werden, sitzen sie da und warten – auf den nächsten Prozess. Dies ist typisch für die traditionellen „Batch and Queue“-Methoden. Warten bedeutet, dass das Produkt das Unternehmen Geld kostet und keinen Mehrwert schafft.
Überproduktion
Die schlimmste der 7 Verschwendungen – da sie auch alle anderen Verschwendungen einschließt. Überproduktion tritt auf, wenn die Prozesse nicht effizient sind. Wenn die Umstellungen zu langsam sind, würde man überproduzieren; wenn die Qualität schlecht ist, würde man wieder überproduzieren, nur für den Fall. Das Problem ist: „Der Kunde will vielleicht 10 Teile, aber wir produzieren 20 Teile und lagern sie…….“.
Die Schwierigkeit besteht darin, dass wertvolle Zeit und Energie in die Produktion von Teilen geflossen ist, die dann in den Lagern herumliegen und Platz verbrauchen, wobei jemand Zeit damit verbringen muss, sie zu bearbeiten und die Bestände zu zählen, und der Kunde hat sie noch nicht einmal gekauft – und das alles auf Kosten des Unternehmens!
Überbearbeitung
Wenn Sie nicht genau wissen, was der Kunde will, wie können Sie dann Ihre Prozesse auf die Bedürfnisse des Kunden abstimmen? Bei der Überbearbeitung geht es darum, Arbeit für den Kunden zu erledigen, die mehr ist, als der Kunde wirklich will. Denken Sie an das Mähen Ihres Rasens – würden Sie jeden Grashalm mit einer Schere abschneiden und ihn dann mit einem Zollstock ausmessen? Natürlich nicht – es reicht, den Rasen mit dem Mäher zu mähen.
Ein anderes Beispiel: Ein Unternehmen, für das ich früher gearbeitet habe, hat Handy-Tastaturen gedruckt. Der Kunde wollte fehlerfreie (mit bloßem Auge zu erkennende) Tastenfelder, aber unsere Inspektoren betrachteten jedes Teil mit einem Augenglas mit 14-facher Vergrößerung! Jede noch so kleine Unvollkommenheit in einem Brillenglas bedeutete, dass das Teil zurückgewiesen wurde, obwohl es bei klarem Licht und mit bloßem Auge perfekt war!
Es überrascht wahrscheinlich nicht, dass das Unternehmen Zeit mit Nacharbeit und Überprüfungen verschwendete, und allein der Ausschuss belief sich auf über 500.000 Pfund pro Jahr bei einem Produkt, das einen Umsatz von 3 Millionen Pfund pro Jahr erzielte!
Mängel
Sie können nicht zweimal einen Mehrwert schaffen! Wenn Sie einen kompletten Auftrag verschrotten, würden Sie nicht zu Ihrem Kunden gehen und 5000 Pfund (oder was auch immer das kostet!) verlangen, um einen Auftrag neu zu bearbeiten, den Sie beim ersten Mal nicht richtig erledigen konnten! Ihr Kunde würde Sie für verrückt halten und woanders hingehen!
Jedes Stückchen Schrott kostet Geld und Zeit – Geld für die Ressourcen, um Personal, Beleuchtung usw. zu bezahlen, um es noch einmal zu machen, bedeutet aber auch, dass Sie einen anderen geplanten Auftrag in der Warteschlange nach hinten schieben müssen, um die Nacharbeit zu erledigen! Das sind alles Kosten und weniger Geld für das Unternehmen.
Jetzt sind Sie dran!
Behalten Sie die 7 Verschwendungen im Hinterkopf, und was noch wichtiger ist, Tim Wood, und versuchen Sie, zehn Minuten lang in der Werkstatt Ihres Büros oder Ihrer Produktionsstätte zu stehen, und notieren Sie, wie oft Sie in diesem Zehn-Minuten-Fenster jede der 7 Verschwendungen sehen.
Schreiben Sie die Beweise auf einen Notizblock und überprüfen Sie dann die Ergebnisse – es ist erstaunlich zu sehen, wie viel Verschwendung es in jedem Prozess gibt.
Wenn Sie jede der 7 Verschwendungen gefunden haben, nehmen Sie sich Zeit für das Team und stellen Sie die folgenden Fragen:
- Könnt ihr sie beseitigen?
- Wenn nein, könnt ihr die NVA-Zeit reduzieren?
- Wenn nein, könnt ihr die NVA-Aktivitäten zusammenfassen?
Macht euch weiter auf die Suche nach Tim Wood und teilt mir eure
Funde mit………………….
Weitere verwandte Artikel:
- Lean Flow
- Kaizen
- Lean Prinzipien
- Lean Werkzeuge
- Lean Six Sigma
- Lean Kultur