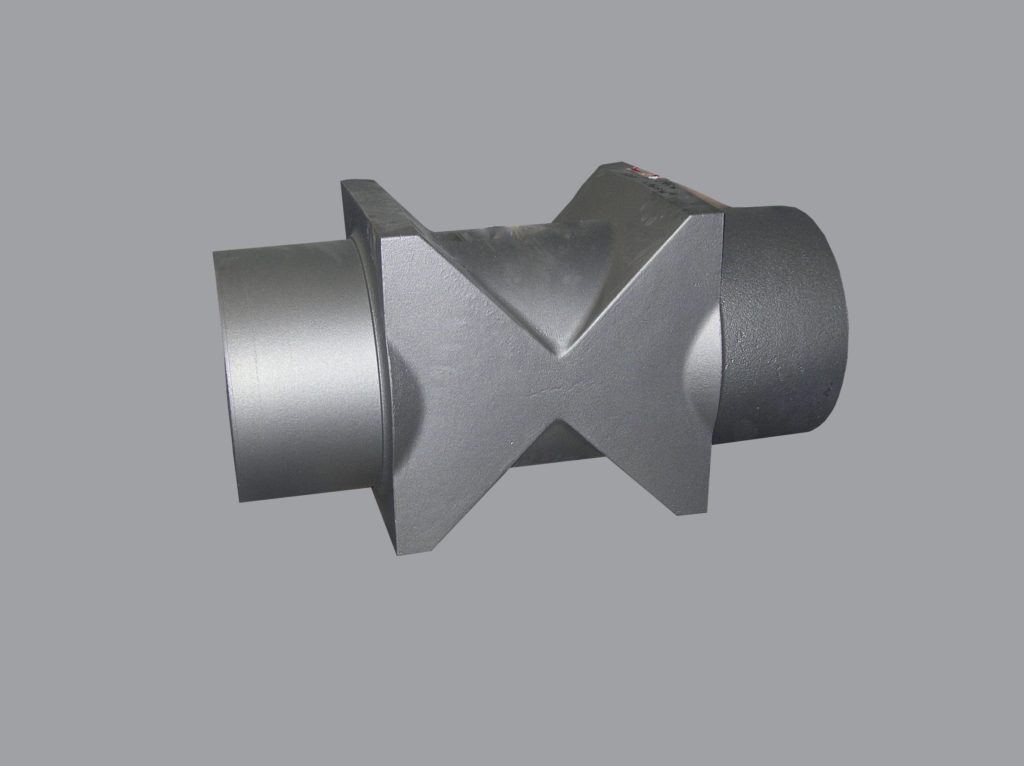
Las aleaciones o metales ferrosos son metales que consisten principalmente en hierro (Fe). El acero es una aleación a base de hierro que suele contener menos de un 1% de carbono, mientras que el hierro suele contener un 2% o más de carbono. El hierro y el acero están ampliamente disponibles, son fuertes, baratos y se les puede dar forma mediante fundición. Las propiedades de las aleaciones ferrosas pueden mejorarse mediante el tratamiento térmico y, en el caso de los aceros, mediante el trabajo (es decir, el laminado o la forja). Los aceros inoxidables se desarrollaron para resistir la corrosión y, por lo general, contienen un 12% o más de cromo y pueden contener níquel en cualquier cantidad, hasta o incluso superando el contenido de cromo, en función de las propiedades mecánicas deseadas y de la aplicación.
Hay varios tipos de acero inoxidable. Al considerar estas aleaciones para su uso en un entorno corrosivo, el método más utilizado para la selección inicial es comparar los índices PREn (número equivalente de resistencia a la picadura) entre los materiales. Esto se calcula utilizando el porcentaje en peso de los elementos de aleación clave presentes en cualquier grado particular de acero inoxidable. La fórmula es:
PREn = % Cr + (3,3 x % Mo) + (16 x % N)
Obviamente, se considera que las aleaciones que contienen las mayores cantidades de cromo, molibdeno y nitrógeno poseen una mejor resistencia a la corrosión por picadura. Esto puede ir acompañado del correspondiente aumento de la resistencia a la tracción y al límite elástico.
Aceros inoxidables ferríticos
Los aceros inoxidables deben su capacidad de resistencia a la corrosión principalmente a la presencia de una película pasiva en su superficie. El cromo es el principal responsable de la formación de esta película pasiva. El hierro deja de oxidarse a partir de un contenido de cromo del 12% aproximadamente. La resistencia a los corrosivos oxidantes aumenta rápidamente con el contenido de cromo hasta aproximadamente el 20%. Sin embargo, a partir de ese nivel, la resistencia aumenta a un ritmo más gradual y decreciente. En consecuencia, muy pocas aleaciones inoxidables contienen más del 27% de cromo. Estas aleaciones se componen principalmente de cromo y hierro, con un bajo contenido de carbono. Las aleaciones se suelen clasificar por su estructura cristalina, que se ve afectada por la química y el procesamiento, incluido el tratamiento térmico. Los aceros inoxidables ferríticos tienen una estructura cristalina principalmente de ferrita.
Aceros inoxidables martensíticos
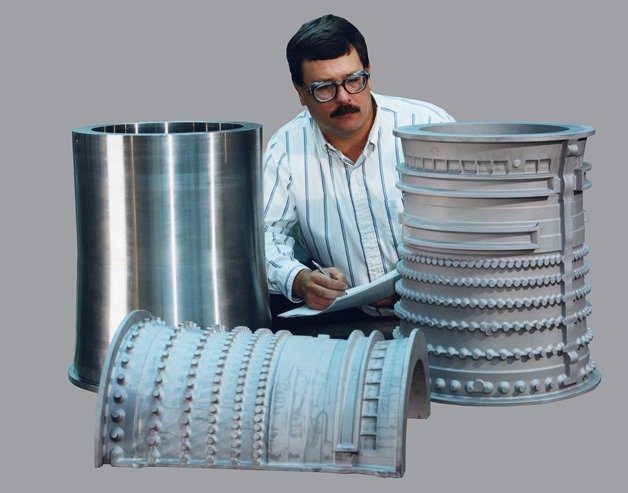
La adición de suficiente carbono a las aleaciones de cromo y hierro da lugar a aleaciones que pueden ser endurecidas y templadas. La resistencia a la corrosión se reduce un poco por el nivel de carbono, pero la reducción se minimiza cuando estas aleaciones están totalmente endurecidas y templadas. Por consiguiente, las aleaciones con más carbono (más del 0,15% C) se utilizan normalmente sólo en estado totalmente templado y revenido. Su estructura tras el enfriamiento rápido a partir de temperaturas superiores a 1600°F / 870°C es principalmente martensítica.
Los grados martensíticos más comunes son: MTEK 410, MTEK 416, MTEK 420, MTEK 431 y MTEK 440.
Aceros inoxidables austeníticos
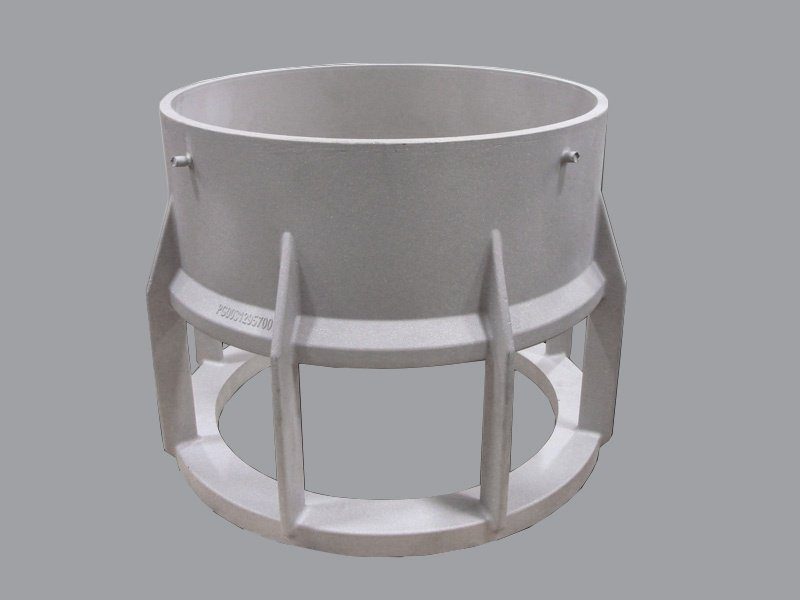
De todos los elementos añadidos a la aleación básica de cromo y hierro, el níquel es el más importante. No sólo mejora la resistencia a la corrosión, sino que también modifica la estructura y las propiedades mecánicas de la aleación. A medida que se añade níquel en cantidades crecientes a una aleación ferrítica de hierro y cromo, la estructura de la aleación cambia de ferrita, pasando por una mezcla de ferrita y austenita, hasta llegar esencialmente a la austenita. La mayoría de los «grados 18-8» (una descripción común de los inoxidables 304 que se componen de aproximadamente un 18% de cromo y un 8% de níquel) se fabrican con cantidades controladas de ferrita para mejorar las características de soldadura y aumentar la resistencia. El cambio de estructura va acompañado de un notable aumento de la ductilidad y la tenacidad. Las aleaciones inoxidables, de estructura predominantemente austenítica, constituyen una familia de aceros inoxidables que son, con mucho, los más utilizados de todos los tipos.
Aceros inoxidables súper austeníticos
En ciertas condiciones agresivas, los grados generales de los aceros inoxidables austeníticos son más susceptibles a las picaduras, la corrosión por hendiduras y el agrietamiento por corrosión bajo tensión. Esto ha conducido al desarrollo y las adiciones a la familia de la austenita, denominada acero inoxidable súper austenítico.
El uso de la súper austenita está creciendo rápidamente debido a las condiciones cambiantes de las industrias de proceso actuales. Se está adoptando un enfoque de «ajustarlo y olvidarlo» para emplear aleaciones que no requieren una sustitución constante y periódica en condiciones como las aguas profundas y las plantas de proceso de circuito cerrado de alta temperatura.
Los aceros inoxidables súper austeníticos contienen altos niveles de cromo y níquel junto con adiciones significativas de molibdeno y nitrógeno. El resultado es una serie de austeníticos. Son hasta un 30% más fuertes que los inoxidables convencionales de la serie 300 y ofrecen una resistencia superior a las picaduras, la corrosión por hendiduras y el agrietamiento por corrosión bajo tensión. Un acero inoxidable austenítico se considera súper austenítico cuando su PREn es superior a 40.
Los grados súper austeníticos más comunes son: MTEK 20, MTEK 20M, MTEK 6XN, y 254SMO®.
Aceros inoxidables dúplex
Los aceros inoxidables dúplex son aleaciones con estructuras generalmente consideradas con partes aproximadamente iguales de austenita y ferrita, siendo una distribución de fases 60/40, 40/60 la envolvente ampliamente considerada como aceptable.
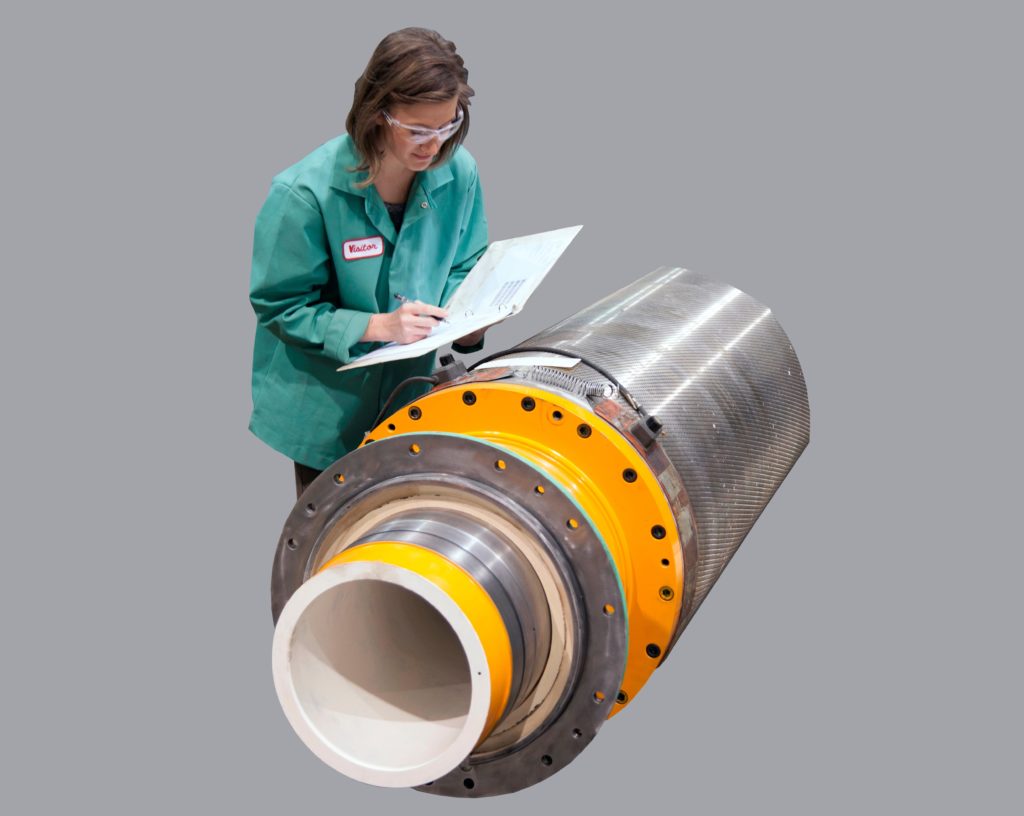
La combinación de austenita/ferrita produce aleaciones con el doble de resistencia que los aceros inoxidables austeníticos convencionales.
Los aceros inoxidables dúplex son prácticamente inmunes al agrietamiento por corrosión bajo tensión (el talón de Aquiles de los aceros inoxidables austeníticos comunes) y son altamente resistentes a la corrosión por picaduras y grietas. Al poseer estas características, no es sorprendente que la mayoría de las aplicaciones (aunque no todas) estén relacionadas con el agua de mar. Los aceros inoxidables dúplex tienen muchos usos en la producción de petróleo y gas en alta mar y en los equipos navales, especialmente en el subsuelo.
Los grados dúplex más comunes son: MTEK 2205, MTEK 29MN / CD4MCuN, Ferralium® 255, Zeron® 100
Aceros inoxidables endurecidos por precipitación (endurecidos por edad)
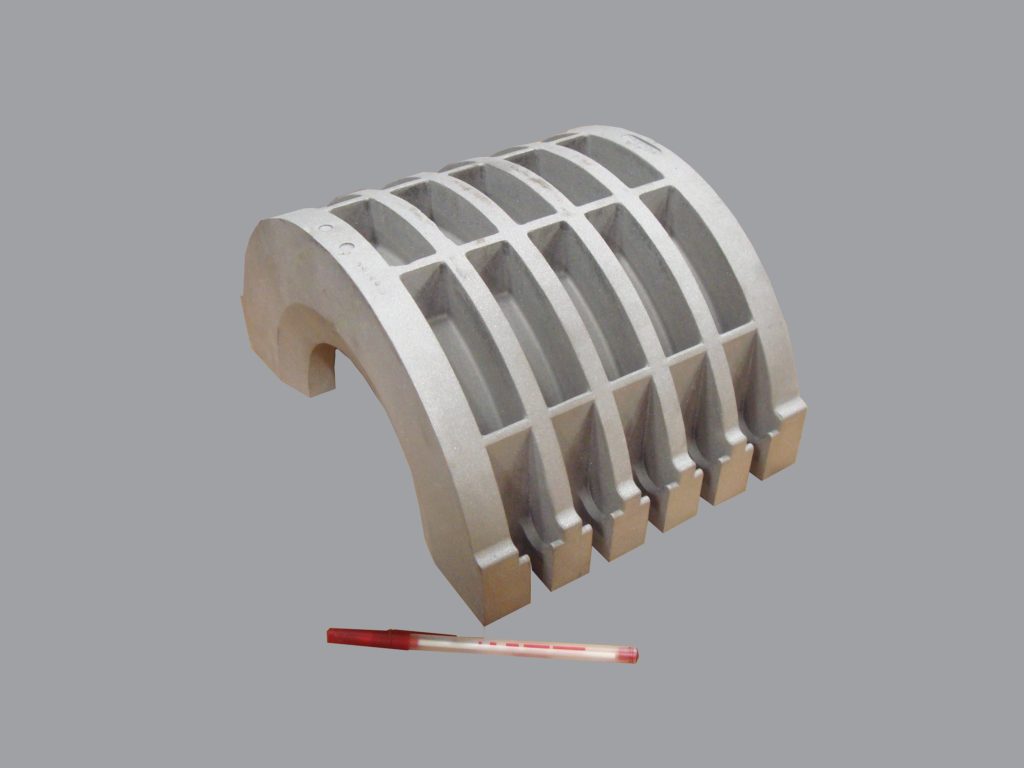
La necesidad de aceros inoxidables que combinen la excelente resistencia a la corrosión de los tipos austeníticos con la capacidad de ser endurecidos por tratamiento térmico llevó al desarrollo de una familia de aceros inoxidables conocidos como tipos PH. Pueden endurecerse por precipitación (envejecimiento) mediante temperaturas bajas (900°F / 480°C), minimizando la distorsión.
Los grados más comunes son: MTEK 17-4PH®, MTEK 15-5PH®, MTEK y 14-4PH®.
¿Tiene preguntas? Póngase en contacto con los expertos en metales ahora.