Comprendere i 7 sprechi ti permette di essere in grado di identificare gli sprechi di processo, sia in un’azienda di produzione che di servizi. Se riesci a vederlo, puoi eliminarlo e quindi aumentare i tuoi livelli di efficienza, produttività e profitto.
Penso che questo sia uno degli aspetti più importanti della Lean manufacturing. Se puoi vederlo e sentirlo, e soprattutto, sentirti a disagio intorno allo spreco, allora lo capisci!
Questo è quello che direbbe il mio vecchio mentore, e ha ragione – se riesci a capirlo, significa che lo capisci – se lo capisci, allora lo puoi eliminare!
Diamo un’occhiata a cosa sono gli sprechi, ma prima una definizione.
NVA & VA
Specificamente, i 7 rifiuti di cui stiamo parlando si riferiscono ai rifiuti di processo. I giapponesi si riferiscono a questo come Muda. Ogni attività che viene condotta in un business è o Valore Aggiunto (VA) o Non Valore Aggiunto (NVA).
Le attività a valore aggiunto sono tutte quelle attività che trasformano fisicamente un prodotto o un servizio agli occhi del cliente – attività che effettivamente aggiungono valore!
Le attività senza valore aggiunto sono tutte quelle attività che vengono svolte, che non aggiungono valore. Alcune possono essere essenziali e possono essere una necessità per fare il lavoro, ma sono ancora NVA, che comprendono i 7 sprechi – Tutti i costi NVA sono sostenuti dall’azienda.
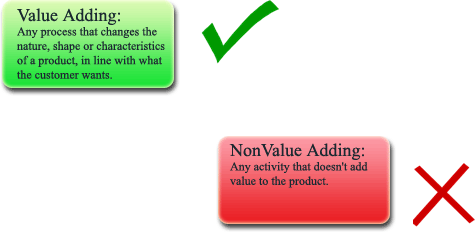
Un esempio
Guardiamo NVA e VA in un semplice flusso di valore qui sotto.
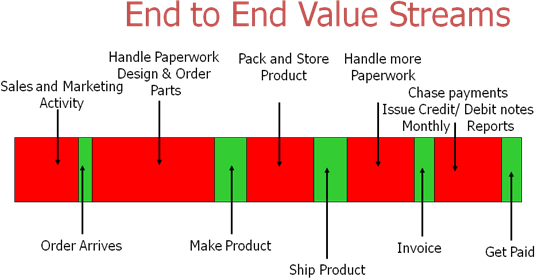
Il diagramma qui sopra mostra il NVA in rosso e il VA in verde. Ovviamente, alcune attività devono essere completate, ma con tutti i compiti, è essenziale chiedersi come si possono ridurre al minimo quelle attività NVA “da fare”.
L’obiettivo finale è quello di eliminare tutti gli NVA (che non sarà mai raggiunto, ma deve comunque essere un obiettivo nella ricerca del miglioramento continuo). Qualsiasi rimozione o riduzione degli sprechi si tradurrà in una riduzione dei tempi di consegna:
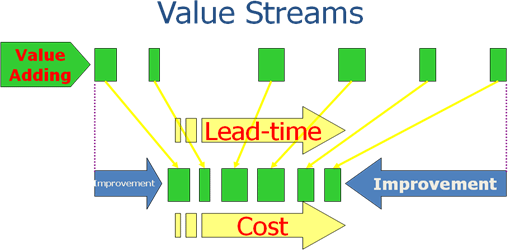
I 7 sprechi in dettaglio
I 7 sprechi sono Non Value Add e devono essere visti come il nemico. Assorbono tempo e costi.
Il modo per ricordarli è pensare a Tim Wood. Questo tizio è in ogni azienda, ed è tua responsabilità dargli la caccia e ridurlo ed eliminarlo come meglio puoi. Assorbe i costi, le spese generali e la liquidità del business.
Ecco TIM WOOD!
T – Trasporto
I – Inventario
M – Movimento
W – Attesa e ritardi
O – Sovrapproduzione
O – Sovrapproduzione
D – Difetti
Trasporto
Il trasporto di prodotti e lavori in corso è necessario, ma deve essere controllato in termini di tempi e distanze. Ogni volta che un prodotto viene spostato, corre il rischio di essere danneggiato, perso, ritardato e così via. Più criticamente, più a lungo un prodotto si sposta, più a lungo non gli viene aggiunto valore, perché non viene fisicamente trasformato. Il trasporto non apporta alcuna trasformazione al prodotto che il consumatore dovrebbe pagare.
Inventario
Produrre qualcosa che sta in attesa del prossimo processo, che non inizia subito, è NVA. Il prodotto è in attesa e non aggiunge valore, seduto su uno scaffale da qualche parte. Il problema è che più inventario c’è, peggio è, perché questo può essere sotto forma di Lavori in corso, materie prime o prodotti finiti.
Il punto è: in ognuna di queste tre forme di inventario, se non è stato venduto, è denaro che è stato vincolato nel materiale, che il cliente non ha ancora comprato- Questo si traduce in un massiccio drenaggio del flusso di cassa!
Spostamento
Simile al trasporto, ma il movimento si riferisce al movimento di operatori e attrezzature. Di nuovo, pensate al fatto che gli operatori che si muovono in giro, cercando e trovando cose non possono essere un valore aggiunto. Lo stesso vale per l’attrezzatura – se spendi del tempo a spostare l’attrezzatura, non puoi usarla per aggiungere valore e fare soldi, inoltre le possibilità di danni aumentano.
Attesa e ritardi
Quando i lavori in corso e le merci non vengono lavorati, stanno lì in attesa – in attesa del prossimo processo. Questo è tipico dei metodi tradizionali ‘Batch and Queue’. L’attesa significa che il prodotto costa all’azienda e non aggiunge valore.
Sovrapproduzione
Il peggiore dei 7 sprechi – poiché incorpora anche tutti gli altri sprechi. La sovrapproduzione appare quando i processi non sono efficienti. Se i cambi sono troppo lenti, si produce troppo; se la qualità è scarsa, di nuovo, si produce troppo, per sicurezza. Il problema è: “il cliente può volere 10 pezzi, per esempio, ma noi produrremo 20 pezzi e li immagazzineremo…….”
La difficoltà è che il tempo e l’energia preziosi sono andati nella produzione di pezzi che stanno in giro a consumare spazio nei magazzini, per cui qualcuno deve passare il tempo a lavorarli e a contare le scorte, e il cliente non li ha nemmeno comprati – Tutto a un costo per l’azienda!
Sopravvivenza
Se non sai esattamente cosa vuole il cliente, come puoi allineare i tuoi processi a ciò che il cliente ha bisogno? La sovraelaborazione consiste nel completare il lavoro per il cliente, che è più di quello che il cliente vuole veramente. Pensate a tagliare il vostro prato – tagliereste ogni filo d’erba con un paio di forbici e poi lo misurereste con un metro? Certo che no -Tagliare il prato con la falciatrice è sufficiente.
Un altro esempio – Una società per cui lavoravo stampava tastiere per cellulari. Il cliente voleva tastiere senza imperfezioni (guardandole a occhio nudo), ma i nostri ispettori guardavano ogni parte con un occhio di vetro con un ingrandimento di 14 volte! Qualsiasi piccola imperfezione in un occhiale significava che il pezzo veniva rifiutato, quando in realtà in piena luce e ad occhio nudo, erano perfetti!
Probabilmente non c’è da stupirsi che l’azienda perdesse tempo in rilavorazioni, ispezioni eccessive, e che gli scarti da soli superassero le 500.000 sterline all’anno su un prodotto che fatturava 3 milioni di sterline all’anno!
Rifiuti
Non si può aggiungere valore due volte! Se si scarta un lavoro completo, non si va dal cliente a chiedere un extra di £5000 (o qualunque sia il costo!) per rilavorare un lavoro che non si è riusciti a fare bene la prima volta! Il tuo cliente penserebbe che sei pazzo e andrebbe altrove!
Ogni pezzo di scarto costa soldi e tempo – Soldi per le risorse per pagare il personale, l’illuminazione, ecc per farlo di nuovo, ma significa anche che si deve spingere un altro lavoro pianificato indietro nella coda al fine di ottenere la rilavorazione fuori! Sono tutti costi e meno soldi per il business.
Ora tocca a te!
Tenendo a mente i 7 sprechi e, cosa più importante, Tim Wood, prova a stare in piedi sul pavimento del tuo ufficio o impianto di produzione per dieci minuti, e annota quante volte vedi ognuno dei 7 sprechi in quella finestra di dieci minuti.
Registra le prove su un blocco note e poi rivedi i risultati: è abbastanza sorprendente vedere quanti sprechi ci sono in ogni processo.
Una volta che hai trovato ognuno dei 7 sprechi, passa del tempo con la squadra e chiedi quanto segue:
- Puoi eliminarlo?
- Se no, puoi ridurre il tempo di NVA?
- Se no, puoi combinare le attività NVA insieme?
Continua la caccia a Tim Wood e fammi sapere le tue
scoperte…………………..
Altri articoli correlati:
- Lean Flow
- Kaizen
- Principi Lean
- Strumenti Lean
- Lean Six Sigma
- Cultura Lean