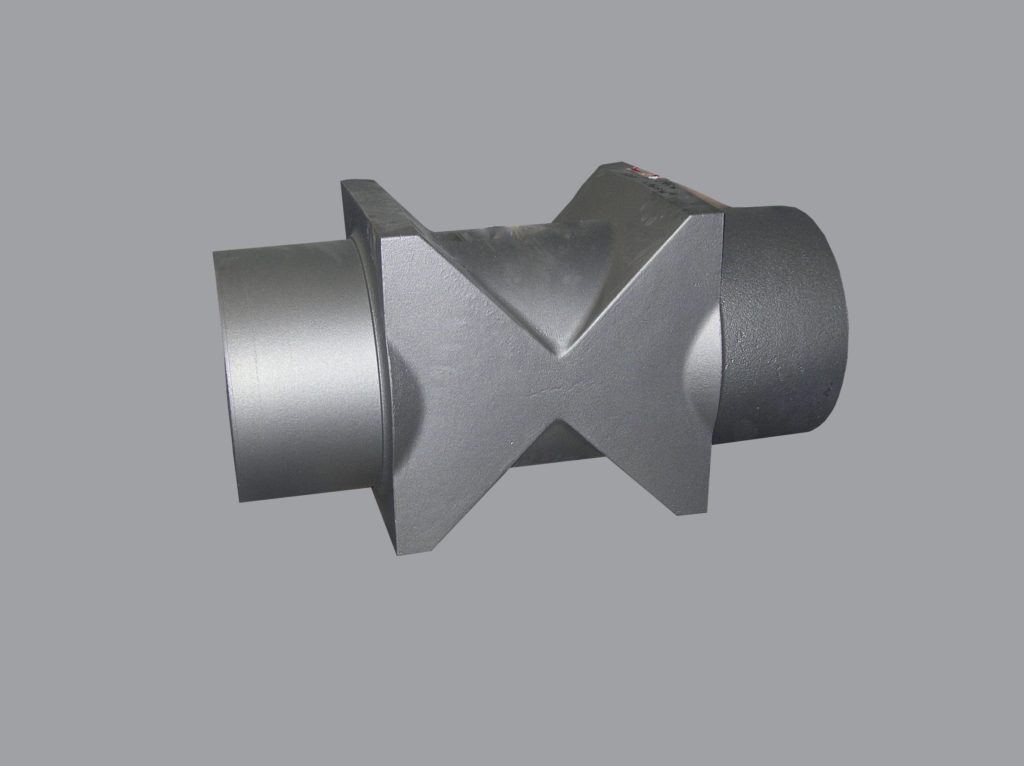
Les alliages ou métaux ferreux sont des métaux constitués principalement de fer (Fe). L’acier est un alliage à base de fer contenant généralement moins de 1% de carbone, alors que le fer contient fréquemment 2% ou plus de carbone. Le fer et l’acier sont largement disponibles, solides, bon marché et peuvent être façonnés par moulage. Les propriétés des alliages ferreux peuvent être améliorées par le traitement thermique et, dans le cas des aciers, par le travail (c’est-à-dire le laminage ou le forgeage). Les aciers inoxydables ont été développés pour résister à la corrosion et contiennent généralement 12% ou plus de chrome et peuvent contenir du nickel en toute quantité jusqu’à ou même dépasser la teneur en chrome en fonction des propriétés mécaniques souhaitées et de l’application.
Il existe plusieurs types d’acier inoxydable. Lorsque l’on envisage d’utiliser ces alliages dans un environnement corrosif, la méthode la plus largement utilisée pour la sélection initiale consiste à comparer les indices PREn (nombre équivalent de résistance à la piqûre) entre les matériaux. Ce chiffre est calculé en utilisant le % en poids des éléments d’alliage clés présents dans toute catégorie particulière d’acier inoxydable. La formule est la suivante :
PREn = % Cr + (3,3 x % Mo) + (16 x % N)
De toute évidence, les alliages contenant les plus grandes quantités de chrome, de molybdène et d’azote sont considérés comme possédant une meilleure résistance à la corrosion par piqûre. Cela peut s’accompagner d’une augmentation correspondante des résistances à la traction et à l’élasticité.
Aciers inoxydables ferritiques
Les aciers inoxydables doivent leur capacité à résister à la corrosion principalement à la présence d’un film passif à leur surface. Le chrome est le principal responsable de la formation de ce film passif. Le fer cesse de rouiller à partir d’une teneur en chrome d’environ 12 %. La résistance aux corrosifs oxydants augmente rapidement avec la teneur en chrome jusqu’à environ 20%. Au-delà de ce niveau, cependant, la résistance augmente à un rythme plus graduel et décroissant. Par conséquent, très peu d’alliages inoxydables contiennent plus de 27 % de chrome. Ces alliages sont composés principalement de chrome et de fer, avec une faible teneur en carbone. Les alliages sont souvent classés en fonction de leur structure cristalline, qui est influencée par la chimie et le traitement, notamment le traitement thermique. Les aciers inoxydables ferritiques ont une structure cristalline principalement en ferrite.
Aciers inoxydables martensitiques
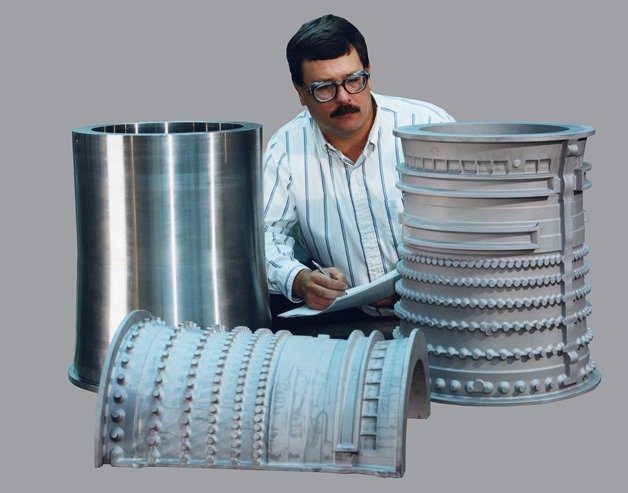
L’ajout de suffisamment de carbone aux alliages de chrome et de fer permet d’obtenir des alliages qui peuvent être durcis et trempés. La résistance à la corrosion est quelque peu réduite par le niveau de carbone, mais cette réduction est minimisée lorsque ces alliages sont entièrement durcis et trempés. Par conséquent, les alliages à forte teneur en carbone (plus de 0,15 % de C) ne sont normalement utilisés qu’à l’état entièrement trempé et revenu. Leur structure lors du refroidissement rapide à partir de températures supérieures à 1600°F / 870°C est principalement martensitique.
Les nuances martensitiques courantes comprennent : MTEK 410, MTEK 416, MTEK 420, MTEK 431 et MTEK 440.
Aciers inoxydables austénitiques
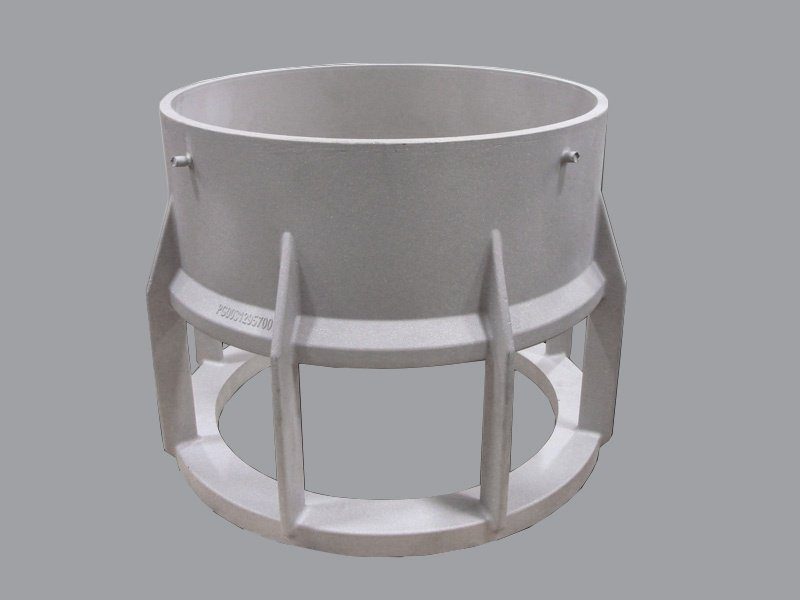
De tous les éléments ajoutés à l’alliage de base de chrome et de fer, le nickel est le plus important. Il améliore non seulement la résistance à la corrosion mais modifie également la structure et les propriétés mécaniques de l’alliage. Lorsque l’on ajoute du nickel en quantités croissantes à un alliage fer/chrome ferritique, la structure de l’alliage passe de la ferrite à l’austénite, en passant par un mélange de ferrite et d’austénite, pour finir par de l’austénite. La plupart des « nuances 18-8 » (une description courante de l’acier inoxydable 304, composé d’environ 18 % de chrome et 8 % de nickel) sont fabriquées avec des quantités contrôlées de ferrite pour améliorer les caractéristiques de soudage et la résistance. La modification de la structure s’accompagne d’une augmentation sensible de la ductilité et de la résistance. Les alliages inoxydables, dont la structure est principalement austénitique, constituent une famille d’aciers inoxydables qui sont de loin les plus utilisés de tous les types.
Aciers inoxydables super austénitiques
Dans certaines conditions agressives, les qualités générales d’acier inoxydable austénitique sont plus sensibles aux piqûres, à la corrosion par crevasses et à la fissuration par corrosion sous contrainte. Cela a conduit au développement et aux ajouts à la famille de l’austénite, appelée acier inoxydable super austénitique.
L’utilisation de la super austénite se développe rapidement en raison des conditions changeantes dans les industries de transformation d’aujourd’hui. Une approche du type « installez-le et oubliez-le » est adoptée pour employer des alliages qui ne nécessitent pas un remplacement constant et régulier dans des conditions telles que l’eau de mer profonde et les installations de traitement en circuit fermé à haute température.
Les aciers inoxydables super austénitiques contiennent des niveaux élevés de chrome et de nickel ainsi que des ajouts significatifs de molybdène et d’azote. Le résultat est une série d’austénitiques. Ils sont jusqu’à 30 % plus solides que les aciers inoxydables conventionnels de la série 300 et offrent une résistance supérieure aux piqûres, à la corrosion par crevasses et à la fissuration par corrosion sous contrainte. Un acier inoxydable austénitique est considéré comme super austénitique lorsque son PREn dépasse 40.
Les nuances super austénitiques courantes comprennent : MTEK 20, MTEK 20M, MTEK 6XN, et 254SMO®.
Aciers inoxydables duplex
Les aciers inoxydables duplex sont des alliages dont les structures sont généralement considérées comme étant constituées de parties approximativement égales d’austénite et de ferrite, une distribution de phases 60/40, 40/60 étant l’enveloppe largement considérée comme acceptable.
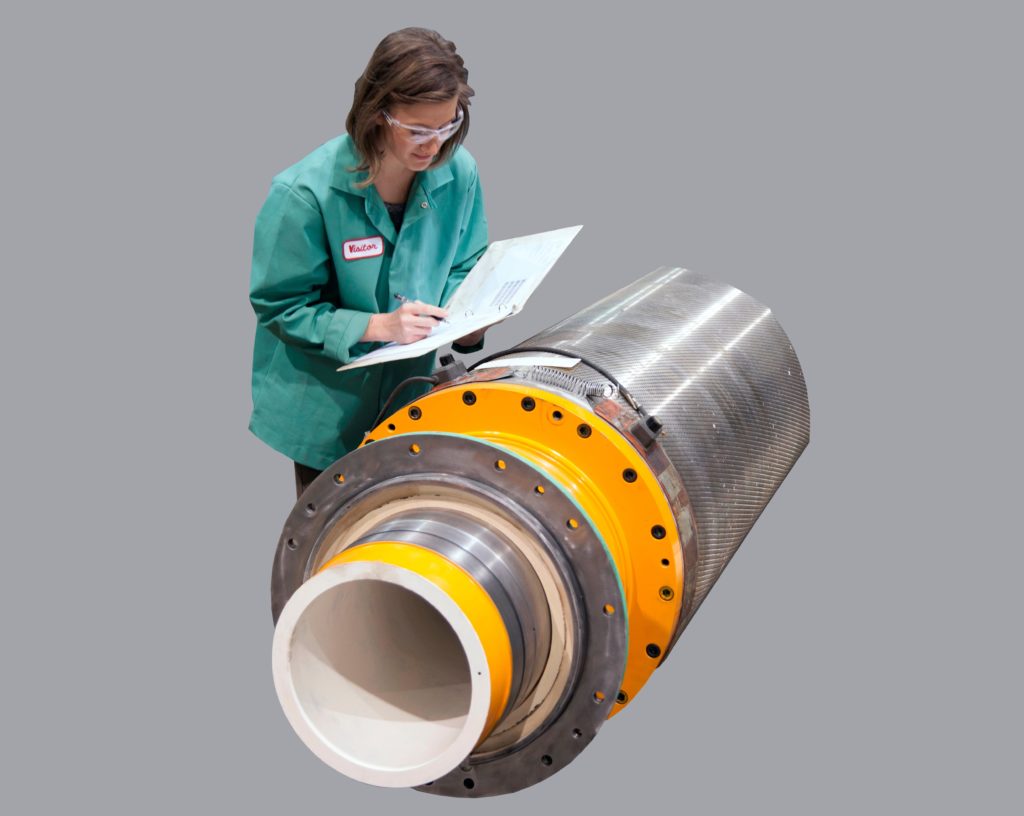
La combinaison austénite/ferrite produit des alliages dont la résistance est deux fois supérieure à celle des aciers inoxydables austénitiques classiques.
Les aciers inoxydables duplex sont pratiquement immunisés contre la fissuration par corrosion sous contrainte (le talon d’Achille des aciers inoxydables austénitiques courants) et sont très résistants à la corrosion par piqûre et par crevasse. Compte tenu de ces caractéristiques, il n’est pas surprenant que la majorité des applications (mais pas toutes) soient liées à l’eau de mer. Les aciers inoxydables duplex ont de nombreuses utilisations dans la production de pétrole et de gaz offshore et dans les équipements de la Marine, en particulier sous la surface.
Les nuances duplex courantes sont : MTEK 2205, MTEK 29MN / CD4MCuN, Ferralium® 255, Zeron® 100
Aciers inoxydables à durcissement par précipitation (durcissement par vieillissement)
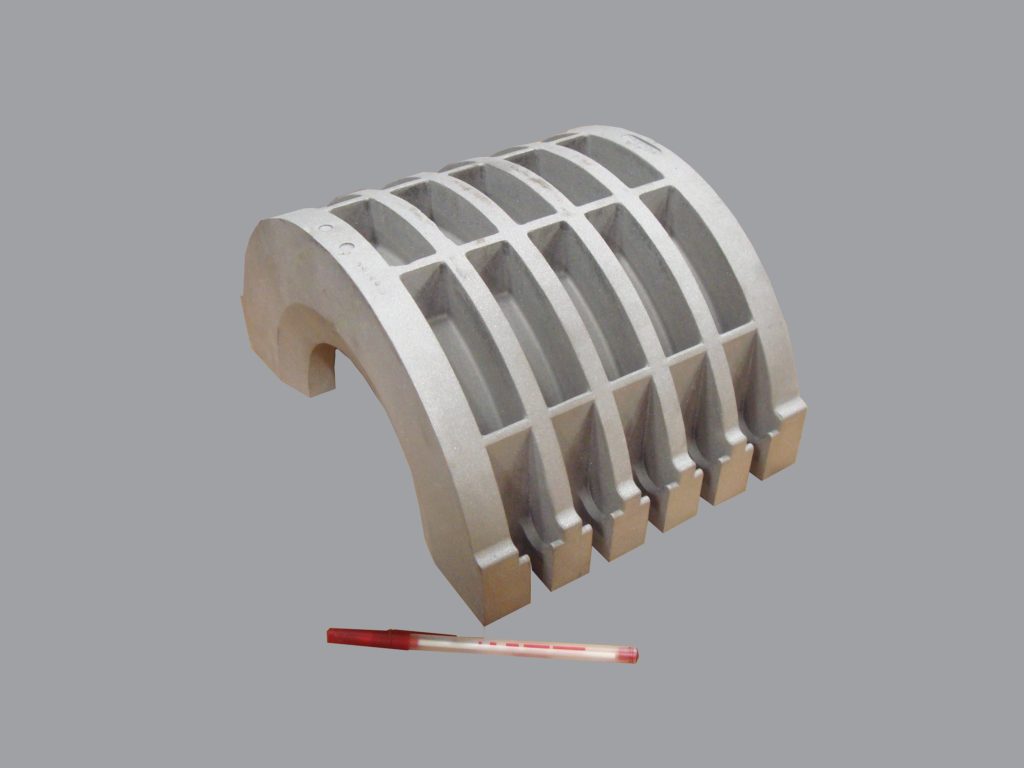
Le besoin d’aciers inoxydables qui combineraient l’excellente résistance à la corrosion des types austénitiques avec la capacité d’être durcis par traitement thermique a conduit au développement d’une famille d’aciers inoxydables connus sous le nom de types PH. Ils peuvent être durcis par précipitation (vieillissement) à basse température (900°F / 480°C), ce qui minimise la distorsion.
Les nuances courantes sont : MTEK 17-4PH®, MTEK 15-5PH®, MTEK et 14-4PH®.
Vous avez des questions ? Contactez les experts en métaux dès maintenant.