Comprendre les 7 gaspillages vous permet d’être capable d’identifier les gaspillages de processus, que ce soit dans une entreprise de fabrication ou de services. Si vous pouvez le voir, vous pouvez l’éliminer et donc augmenter votre efficacité, votre productivité et vos niveaux de profit.
Je pense que c’est l’un des aspects les plus importants du Lean manufacturing. Si vous pouvez le voir et le sentir, et plus important encore, vous sentir mal à l’aise autour du gaspillage, alors vous l’obtenez !
C’est ce que dirait mon vieux mentor, et il a raison – si vous pouvez l’obtenir, cela signifie que vous le comprenez – si vous le comprenez, alors vous pouvez l’éliminer !
Regardons ce que sont les déchets, mais d’abord une définition.
NVA & VA
Spécifiquement, les 7 déchets dont nous parlons font référence aux déchets de processus. Les Japonais les désignent sous le nom de Muda. Chaque activité menée dans une entreprise est soit à valeur ajoutée (VA), soit sans valeur ajoutée (NVA).
Les activités à valeur ajoutée sont toutes celles qui transforment physiquement un produit ou un service aux yeux du client – des activités qui ajoutent réellement de la valeur !
Les activités sans valeur ajoutée sont toutes les activités qui sont menées, qui n’ajoutent pas de valeur. Certaines peuvent être essentielles et constituer une nécessité pour faire le travail, mais restent des NVA, qui englobent les 7 gaspillages – Tous les coûts des NVA sont supportés par l’entreprise.
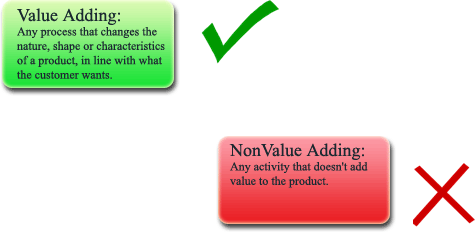
Un exemple
Regardons la NVA et la VA dans un simple flux de valeur ci-dessous.
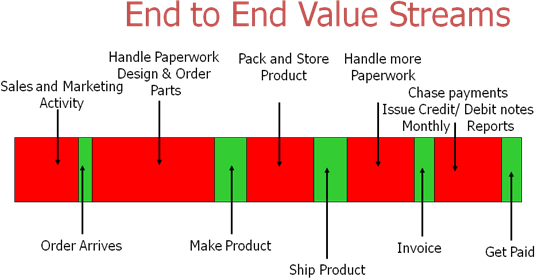
Le diagramme ci-dessus démontre la NVA en rouge et la VA en vert.
Le but est de supprimer autant de NVA que possible. Il est évident que certaines activités doivent être réalisées, mais avec toutes les tâches, il est essentiel de se demander comment vous pouvez réduire au minimum ces tâches NVA » indispensables « .
Le but ultime est de supprimer tous les NVA (ce qui ne sera jamais atteint, mais doit rester un objectif dans la poursuite de l’amélioration continue). Toute suppression ou réduction des déchets se traduira par un raccourcissement des délais d’exécution :
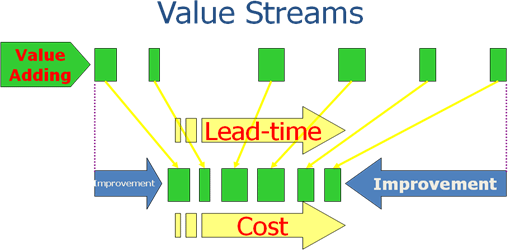
Les 7 gaspillages en détail
Les 7 gaspillages sont des Non Value Add et doivent être considérés comme l’ennemi. Ils absorbent du temps, et des coûts.
La façon de s’en souvenir est de penser à Tim Wood. Ce type est dans toutes les entreprises, et il est de votre responsabilité de le traquer, de le réduire et de l’éliminer du mieux que vous pouvez. Il absorbe les coûts, les frais généraux et les liquidités de l’entreprise.
Voici donc TIM WOOD !
T – Transport
I – Inventaire
M – Mouvement
W – Attente et retards
O – Surproduction.
O – Surtransformation
D – Défauts
Transport
Le transport des produits et des travaux en cours est nécessaire, mais il doit être contrôlé en termes de temps et de distance. Chaque fois qu’un produit est déplacé, il court le risque d’être endommagé, perdu, retardé, et ainsi de suite. Plus grave encore, plus un produit se déplace longtemps, plus il n’y a pas de valeur ajoutée, car il n’est pas physiquement transformé. Le transport n’apporte aucune transformation au produit que le consommateur est censé payer.
Inventaire
Produire quelque chose pour qu’il reste assis et attende le processus suivant, qui ne démarre pas tout de suite, c’est de la NVA. Le produit attend et n’apporte aucune valeur ajoutée, assis sur un rayonnage quelque part. Le problème est que plus l’inventaire est important, pire c’est, car cela peut être sous la forme de travaux en cours, de matières premières ou de produits finis.
Le point est le suivant : dans n’importe laquelle de ces trois formes d’inventaire, s’il n’a pas été vendu, c’est de l’argent qui a été immobilisé dans le matériel, que le client n’a pas encore acheté- Ceux-ci résultent en une ponction massive sur le flux de trésorerie !
Mouvement
Similaire au transport, mais le mouvement se réfère au mouvement de l’opérateur et de l’équipement. Encore une fois, pensez au fait que les opérateurs qui se déplacent, cherchent et trouvent des choses ne peuvent pas ajouter de la valeur. Il en va de même pour l’équipement – si vous passez du temps à balloter l’équipement, vous ne pouvez pas l’utiliser pour ajouter de la valeur et faire de l’argent, et en plus les chances de dommages augmentent.
Attente et retards
Lorsque les travaux en cours et les marchandises ne sont pas travaillés, ils restent là à attendre – attendre le prochain processus. Cette situation est typique des méthodes traditionnelles de » lots et de files d’attente « . L’attente signifie que le produit coûte de l’argent à l’entreprise et n’ajoute pas de valeur.
Surproduction
Le pire des 7 gaspillages – car il incorpore également tous les autres gaspillages. La surproduction apparaît lorsque les processus ne sont pas efficaces. Si les changements sont trop lents, on surproduit ; si la qualité est mauvaise, là encore, on surproduit, au cas où. Le problème est le suivant : « le client peut vouloir 10 pièces, par exemple, mais nous allons produire 20 pièces et les stocker……. ».
La difficulté est que du temps et de l’énergie précieux ont été consacrés à produire des pièces qui restent là à consommer de l’espace dans les magasins, ce qui fait que quelqu’un doit passer du temps à les traiter et à compter les stocks, alors que le client ne les a même pas achetées – Tout cela à un coût pour l’entreprise !
Surtraitement
Si vous ne savez pas exactement ce que le client veut, comment pouvez-vous aligner vos processus sur ce dont le client a besoin ? Le surtraitement consiste à compléter le travail pour le client, ce qui est plus que ce que le client veut vraiment. Pensez à la tonte de votre pelouse : couperiez-vous chaque brin d’herbe avec une paire de ciseaux pour ensuite le mesurer avec une règle ? Bien sûr que non -Tondre la pelouse avec la tondeuse est suffisant.
Autre exemple – Une entreprise pour laquelle je travaillais imprimait des claviers de téléphones portables. Le client voulait des claviers sans imperfections (en les regardant à l’œil nu), mais nos inspecteurs regardaient chaque pièce avec un verre oculaire d’un grossissement de 14 fois ! Toute légère imperfection dans une lunette signifiait que la pièce était rejetée, alors qu’en fait, en lumière claire et à l’œil nu, elles étaient parfaites !
Il n’est probablement pas surprenant que l’entreprise perdait du temps en retouches, en inspections excessives, et que les rejets seuls représentaient plus de 500 000 £ par an sur un produit qui rapportait 3 millions de £ par an !
Défauts
Vous ne pouvez pas ajouter de la valeur deux fois ! Si vous mettez au rebut un travail complet, vous n’iriez pas demander à votre client 5 000 £ supplémentaires (ou quel que soit le coût !) pour retraiter un travail que vous n’avez pas pu faire correctement du premier coup ! Votre client penserait que vous êtes fou et irait ailleurs !
Chaque morceau de rebut coûte de l’argent et du temps – De l’argent pour la ressource pour payer le personnel, l’éclairage, etc. pour le refaire, mais cela signifie aussi que vous devez repousser un autre travail planifié dans la file d’attente afin de sortir la reprise ! C’est tout un coût et moins d’argent pour l’entreprise.
Maintenant votre tour !
En gardant les 7 gaspillages à l’esprit, et plus important encore, Tim Wood, essayez de vous tenir dans l’atelier de votre bureau ou de votre usine de fabrication pendant dix minutes, et notez combien de fois vous voyez chacun des 7 gaspillages dans cette fenêtre de dix minutes.
Enregistrez les preuves sur un bloc-notes, puis examinez les résultats.Il est assez étonnant de voir à quel point il y a du gaspillage dans chaque processus.
Une fois que vous avez trouvé chacun des 7 gaspillages, passez du temps avec l’équipe et posez les questions suivantes :
- Pouvez-vous l’éliminer ?
- Si non, pouvez-vous réduire le temps de NVA ?
- Si non, pouvez-vous combiner les activités de NVA ensemble ?
Poursuivez la chasse à Tim Wood et faites-moi part de vos
trouvailles……………………
Autres articles connexes:
- Lean Flow
- Kaizen
- Principesean
- Outilsean
- Lean Six Sigma
- Cultureean
.