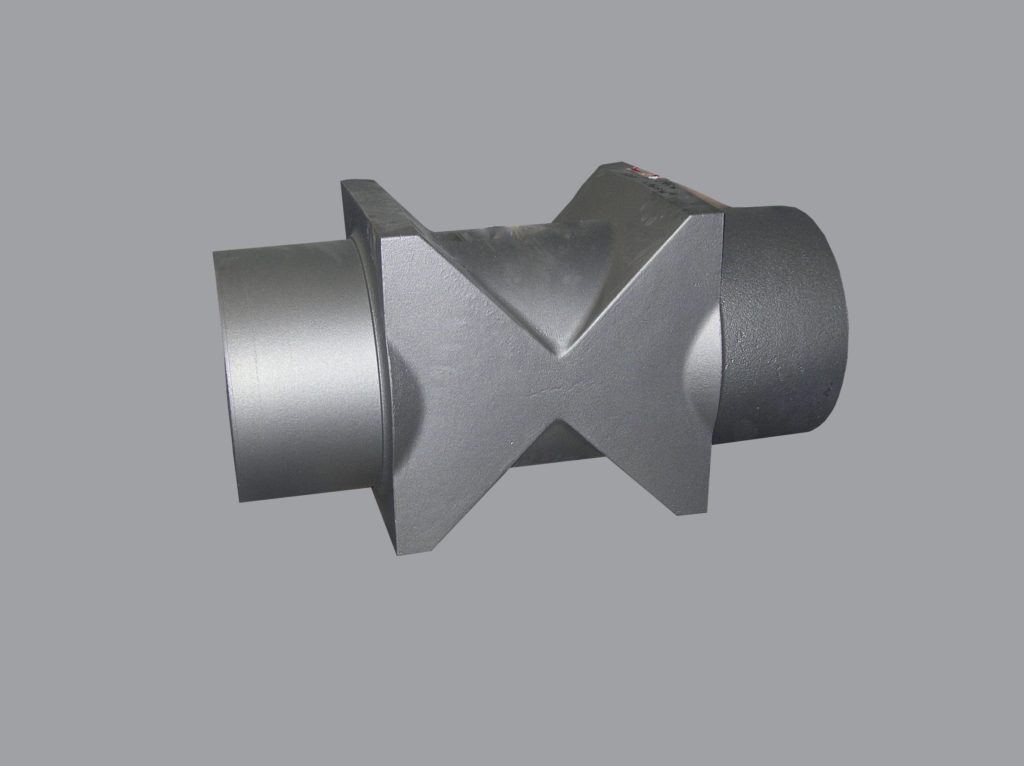
Stopy żelaza lub metale żelazne są metalami, które składają się głównie z żelaza (Fe). Stal jest stopem na bazie żelaza, zawierającym zazwyczaj mniej niż 1% węgla, podczas gdy żelazo często zawiera 2% lub więcej węgla. Żelazo i stal są powszechnie dostępne, mocne, tanie i mogą być kształtowane przez odlewanie. Właściwości stopów żelaza mogą być poprawione przez obróbkę cieplną, a w przypadku stali, przez obróbkę (tj. walcowanie lub kucie). Stale nierdzewne zostały opracowane, aby oprzeć się korozji i zazwyczaj zawierają 12% lub więcej chromu i mogą zawierać nikiel w dowolnej ilości do lub nawet przekraczającej zawartość chromu w oparciu o właściwości mechaniczne pożądane i application.
Istnieje kilka rodzajów stali nierdzewnej. Przy rozważaniu tych stopów do stosowania w środowisku korozyjnym, najbardziej powszechnie stosowaną metodą wstępnego wyboru jest porównanie ocen PREn (równoważna liczba odporności na korozję wżerową) w różnych materiałach. Jest to obliczane przy użyciu % wagowych kluczowych pierwiastków stopowych obecnych w każdym konkretnym gatunku stali nierdzewnej. Wzór jest następujący:
PREn = % Cr + (3.3 x % Mo) + (16 x % N)
Oczywiście, stopy zawierające najwyższe ilości chromu, molibdenu i azotu są uważane za posiadające lepszą odporność na korozję wżerową. Może to być połączone z odpowiednim wzrostem wytrzymałości na rozciąganie i plastyczności.
Ferrytyczne stale nierdzewne
Stale nierdzewne zawdzięczają swoją zdolność do oparcia się korozji przede wszystkim do obecności pasywnego filmu na ich powierzchni. Chrom jest głównie odpowiedzialny za tworzenie tego pasywnego filmu. Żelazo przestaje rdzewieć przy około 12% zawartości chromu. Odporność na utleniające substancje korozyjne wzrasta gwałtownie wraz z zawartością chromu do około 20%. Powyżej tego poziomu, jednak, odporność wzrasta w bardziej stopniowe i malejące tempo. W związku z tym, bardzo niewiele stopów nierdzewnych zawierają więcej niż 27% chromu. Stopy te składają się głównie z chromu i żelaza, z niską zawartością węgla. Stopy są często kategoryzowane przez ich strukturę krystaliczną, która jest pod wpływem chemii i przetwarzania, w tym obróbki cieplnej. Ferrytyczne stale nierdzewne mają strukturę krystaliczną, która jest głównie ferrytowa.
Martenzytyczne stale nierdzewne
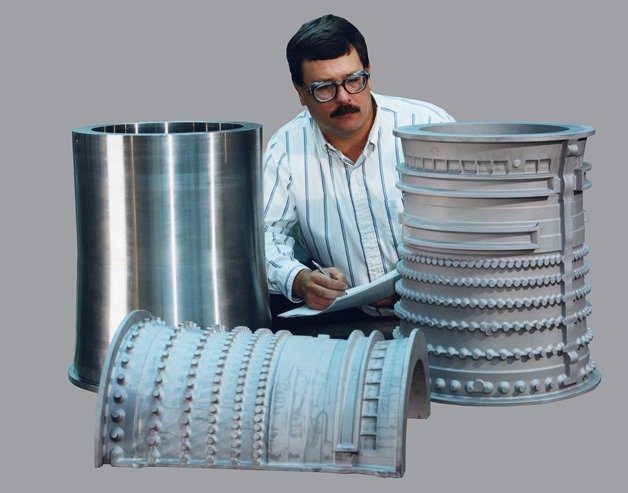
Dodanie wystarczającej ilości węgla do stopów chromu i żelaza skutkuje stopami, które mogą być hartowane i odpuszczane. Odporność na korozję jest nieco zmniejszona przez poziom węgla, ale zmniejszenie jest zminimalizowane, gdy te stopy są w pełni hartowane i odpuszczane. W związku z tym, stopy o wyższej zawartości węgla (powyżej 0,15% C) są zwykle używane tylko w stanie w pełni zahartowanym i odpuszczonym. Ich struktura przy szybkim chłodzeniu z temperatur powyżej 1600°F / 870°C jest głównie martenzytyczna.
Wspólne gatunki martenzytyczne obejmują: MTEK 410, MTEK 416, MTEK 420, MTEK 431, i MTEK 440.
Austenityczne stale nierdzewne
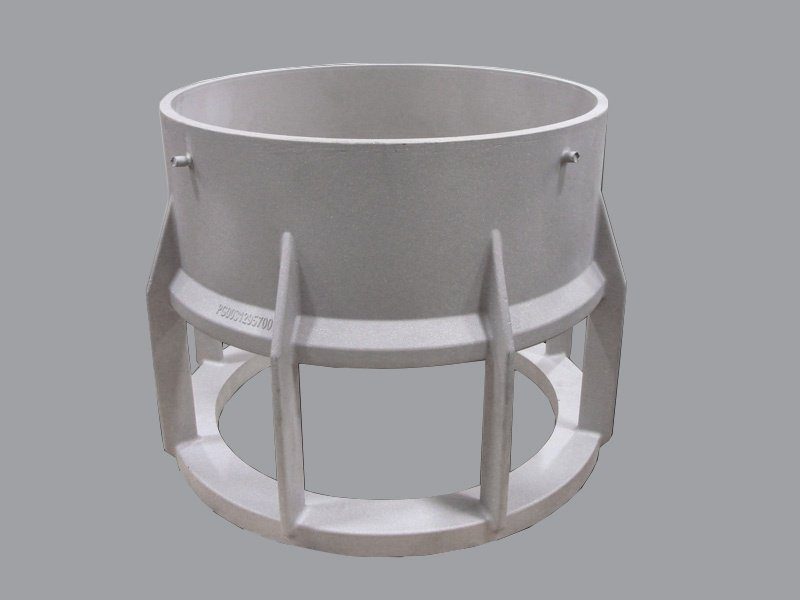
Wśród wszystkich pierwiastków dodawanych do podstawowego stopu chromu i żelaza, nikiel jest najważniejszy. To nie tylko poprawia odporność na korozję, ale także zmienia strukturę stopu i właściwości mechaniczne. Ponieważ nikiel jest dodawany w coraz większych ilościach do ferrytycznego stopu żelaza i chromu, struktura stopu zmienia się z ferrytu, przez mieszany ferryt i austenit, do zasadniczo całego austenitu. Większość „18-8 klas” (wspólny opis 304 nierdzewnej, która składa się z około 18% chromu i 8% niklu) są wykonane z kontrolowaną ilością ferrytu dla lepszych właściwości spawalniczych i wyższej wytrzymałości. Zmiana struktury towarzyszy wyraźny wzrost plastyczności i ciągliwości. Stopy nierdzewne, głównie austenityczne w strukturze, tworzą rodzinę stali nierdzewnych, które są zdecydowanie najczęściej używane ze wszystkich typów.
Super Austenitic Stainless Steels
Pod pewnymi agresywnymi warunkami, ogólne gatunki austenitycznej stali nierdzewnej są bardziej podatne na wżery, korozję szczelinową i korozję naprężeniową. Doprowadziło to do rozwoju i dodatków do rodziny austenitu, określane jako super austenitycznej stali nierdzewnej.
Użycie super austenitu szybko rośnie ze względu na zmieniające się warunki w dzisiejszym przemyśle procesowym. A „dopasować i zapomnieć” podejście jest przyjęty do stosowania stopów, które nie wymagają stałej, regularnej wymiany w warunkach, takich jak głębokiej wody morskiej i wysokiej temperatury zamkniętych zakładów procesowych.
Super austenityczne stale nierdzewne zawierają wysoki poziom chromu i niklu wraz ze znacznymi dodatkami molibdenu i azotu. Rezultatem jest seria austenitycznych. Są one do 30% silniejsze niż konwencjonalne 300 serii nierdzewnej i oferują doskonałą odporność na wżery, korozję szczelinową i korozję naprężeniową pęknięć. Austenityczna stal nierdzewna jest uważana za super austenityczne, gdy jego PREn przekracza 40.
Common super austenityczne klasy obejmują: MTEK 20, MTEK 20M, MTEK 6XN, i 254SMO®.
Stale nierdzewne typu duplex
Stale nierdzewne typu duplex są stopami o strukturze ogólnie uważanej za w przybliżeniu równe części austenitu i ferrytu, przy czym rozkład faz 60/40, 40/60 jest obwiednią powszechnie uważaną za dopuszczalną.
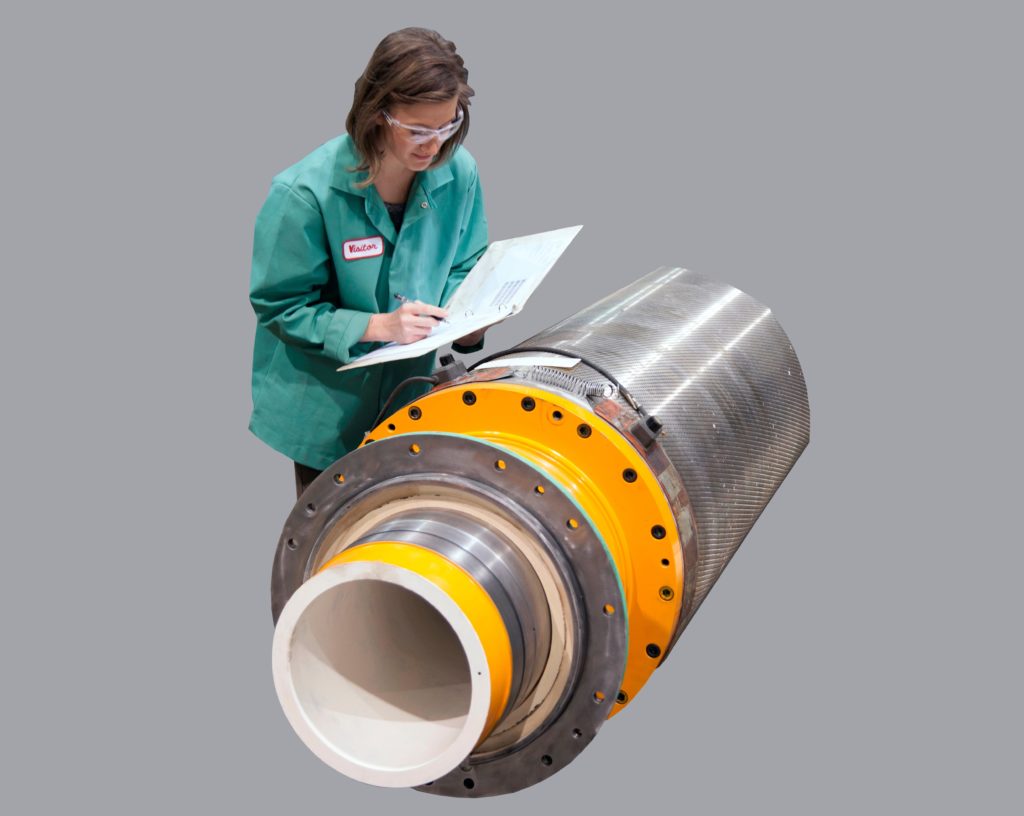
Kombinacja austenitu / ferrytu produkuje stopy o dwukrotnie większej wytrzymałości niż konwencjonalne austenityczne stale nierdzewne.
Stale nierdzewne Duplex są praktycznie odporne na korozję naprężeniową (pięta Achillesa wspólnych austenitycznych stali nierdzewnych) i są bardzo odporne na korozję wżerową i szczelinową. Posiadanie tych cech, to nie jest zaskakujące, aby znaleźć większość (ale w żadnym wypadku nie wszystkie) aplikacje są związane z wodą morską. Stale nierdzewne duplex mają dużo zastosowań w produkcji ropy naftowej i gazu na morzu i sprzętu Naval, zwłaszcza podpowierzchniowych.
Common duplex gatunki są: MTEK 2205, MTEK 29MN / CD4MCuN, Ferralium® 255, Zeron® 100
Stale nierdzewne utwardzane przez wytrącanie (utwardzane wiekiem)
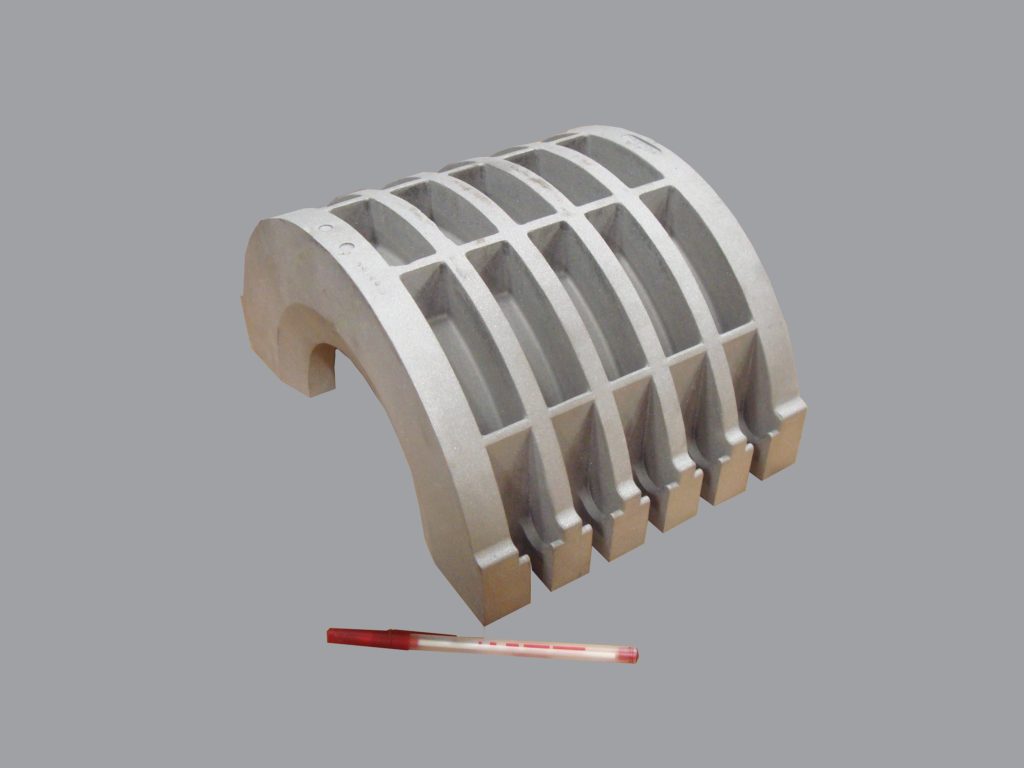
Potrzeba stali nierdzewnych, które połączyłyby doskonałą odporność na korozję typów austenitycznych ze zdolnością do hartowania przez obróbkę cieplną doprowadziła do rozwoju rodziny stali nierdzewnych znanych jako typy PH. Mogą one być utwardzane przez wytrącanie (wiek) w niskich temperaturach (900°F / 480°C), minimalizując zniekształcenia.
Powszechne gatunki to: MTEK 17-4PH®, MTEK 15-5PH®, MTEK i 14-4PH®.
Masz pytania? Skontaktuj się z ekspertami ds. metali już teraz.