Med förståelse för de 7 avfallsslagen kan du identifiera processavfall, oavsett om det rör sig om ett tillverknings- eller tjänsteföretag. Om du kan se det kan du eliminera det och därmed öka din effektivitet, produktivitet och vinstnivå.
Jag anser att detta är en av de viktigaste aspekterna av Lean Manufacturing. Om du kan se det och känna det, och ännu viktigare, känna dig obekväm när det gäller slöseri, då får du det!
Det är vad min gamla mentor skulle säga, och han har rätt – om man kan få ”det” betyder det att man förstår ”det” – om man förstår ”det” kan man eliminera det!
Låt oss ta en titt på vad avfall är, men först en definition.
NVA & VA
Specifikt avser de 7 avfallsslag vi talar om processavfall. Japanerna kallar detta för Muda. Varje verksamhet som bedrivs i ett företag är antingen mervärde (VA) eller icke mervärde (NVA).
Value Add-aktiviteter är alla de aktiviteter som fysiskt förändrar en produkt eller tjänst i kundens ögon – aktiviteter som faktiskt tillför värde!
Non Value Add activities är alla de aktiviteter som genomförs och som inte tillför något värde. Vissa kan vara viktiga och nödvändiga för att utföra jobbet, men de är ändå icke-nyttiga aktiviteter, som omfattar de sju slöserierna – alla icke-nyttiga kostnader bärs av företaget.
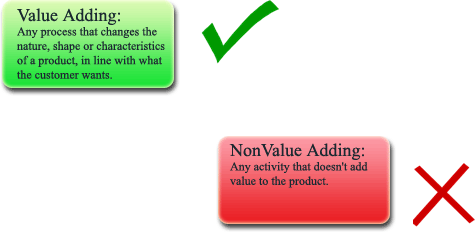
Ett exempel
Låt oss titta på NVA och VA i ett enkelt värdeflöde nedan.
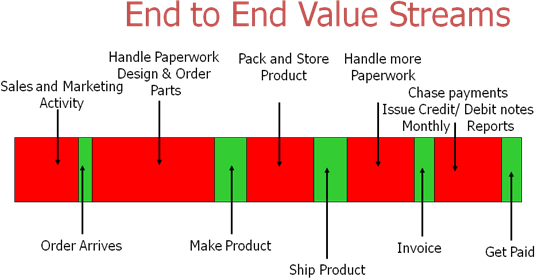
Diagrammet ovan visar NVA i rött och VA i grönt.
Syftet är att ta bort så mycket NVA som möjligt. Självklart måste vissa aktiviteter genomföras, men när det gäller alla uppgifter är det viktigt att fråga sig hur man kan minska dessa ”måste-uppgifter” NVA till ett minimum.
Det ultimata målet är att ta bort all NVA (vilket aldrig kommer att uppnås, men måste ändå vara ett mål i strävan efter ständiga förbättringar). Varje borttagning eller minskning av avfall kommer att resultera i kortare ledtider:
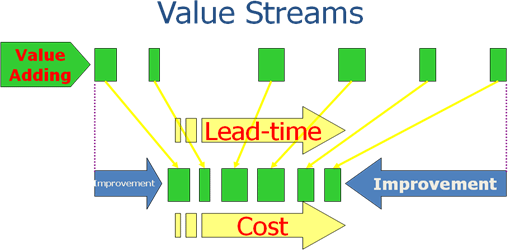
De 7 slöserierna i detalj
De 7 slöserierna är icke-värdeskapande och måste ses som fienden. De absorberar tid och kostnader.
Sättet att komma ihåg dem är att tänka på Tim Wood. Den här killen finns i alla företag, och det är ditt ansvar att jaga honom och minska och eliminera så gott du kan. Han absorberar kostnader, overheadkostnader och kontanter i verksamheten.
Här är alltså TIM WOOD!
T – Transport
I – Inventering
M – Förflyttning
W – Väntan och förseningar
O – Överproduktion.
O – Överproduktion
D – Defekter
Transport
Transport av produkter och pågående arbeten är nödvändig, men den måste kontrolleras när det gäller tid och avstånd. Varje gång en produkt flyttas riskerar den att skadas, gå förlorad, bli försenad och så vidare. Ju längre en produkt flyttas, desto mer kritiskt är det att det inte tillförs något värde till den, eftersom den inte omvandlas fysiskt. Transporten gör ingen omvandling av den produkt som konsumenten ska betala för.
Inventarier
Produktion av något som ska sitta och vänta på nästa process, som inte startar direkt, är NVA. Produkten väntar och tillför inget värde när den ligger på en arbetshylla någonstans. Problemet är att ju mer lager desto värre är det, eftersom det kan vara i form av pågående arbeten, råmaterial eller färdiga varor.
Punkten är att i någon av dessa tre former av lager, om det inte har sålts, är det kontanter som har bundits i materialet, som kunden ännu inte har köpt – detta resulterar i ett massivt dränering av kassaflödet!
Förflyttning
Samma som för transport, men med förflyttning avses förflyttning av operatör och utrustning. Tänk återigen på att operatörer som rör sig runt, söker och hittar saker inte kan skapa mervärde. Samma sak med utrustning – om du spenderar tid på att flytta runt utrustning kan du inte använda den för att skapa mervärde och tjäna pengar, dessutom ökar risken för skador.
Vänta och förseningar
När pågående arbeten och varor inte bearbetas sitter de där och väntar – i väntan på nästa process. Detta är typiskt för traditionella ”Batch and Queue”-metoder. Väntan innebär att produkten kostar företaget pengar och inte tillför något mervärde.
Överproduktion
Det värsta av de sju slöserierna – eftersom det också innefattar alla andra slöserier. Överproduktion uppstår när processerna inte är effektiva. Om omställningarna är för långsamma skulle man överproducera, och om kvaliteten är dålig skulle man återigen överproducera, för säkerhets skull. Problemet är att ”kunden kanske vill ha t.ex. 10 delar, men vi kommer att producera 20 delar och lagra dem” (…….).
Svårigheten är att värdefull tid och energi har gått åt till att producera delar som sitter och tar plats i lagren, varvid någon måste ägna tid åt att bearbeta dem och räkna dem i lager, och kunden har inte ens köpt dem – allt till en kostnad för företaget!
Överbehandling
Om du inte vet exakt vad kunden vill ha, hur kan du då anpassa dina processer till vad kunden behöver? Överbearbetning handlar om att slutföra arbete åt kunden, vilket är mer än vad kunden egentligen vill ha. Tänk på att klippa gräsmattan – skulle du klippa varje grässtrå med en sax och sedan mäta det med en måttstock? Naturligtvis inte – det räcker att klippa gräsmattan med gräsklipparen.
Ett annat exempel: Ett företag som jag arbetade för brukade skriva ut tangentbord för mobiltelefoner. Kunden ville ha nyckelfelare utan fläckar (om man tittar på dem med blotta ögat), men våra inspektörer tittade på varje del med ett glasögonglas med 14 gångers förstoring! Varje liten defekt i ett glasögon innebar att delen avvisades, när de i själva verket i klart ljus och med blotta ögat var perfekta!
Det kommer förmodligen inte som någon överraskning att företaget slösade tid på omarbetning, överinspektion och att enbart kassationer uppgick till över 500 000 pund per år på en produkt som omsatte 3 miljoner pund per år!
Fel
Du kan inte skapa mervärde två gånger! Om du skrotar ett helt jobb skulle du inte gå till din kund och be om 5 000 pund extra (eller vad det nu kostar!) för att bearbeta ett jobb som du inte kunde göra rätt första gången! Din kund skulle tro att du är galen och gå någon annanstans!
Varje skrot kostar pengar och tid – pengar för att betala personal, belysning osv. för att göra om det, men det innebär också att du måste skjuta ett annat planerat jobb bakåt i kön för att få ut omarbetningen! Det är en total kostnad och mindre pengar för företaget.
Nu är det din tur!
För att hålla de sju slöserierna i åtanke, och ännu viktigare, Tim Wood, kan du försöka stå på verkstadsgolvet på ditt kontor eller i din tillverkningsanläggning i tio minuter och notera hur många gånger du ser vart och ett av de sju slöserierna under de tio minuterna.
Registrera bevisen på ett anteckningsblock och gå sedan igenom resultaten.Det är ganska häpnadsväckande att se hur mycket slöseri det finns i varje process.
När du har hittat vart och ett av de sju slöserierna kan du tillbringa tid med teamet och ställa följande frågor:
- Kan ni eliminera det?
- Om inte, kan ni minska NVA-tiden?
- Om inte, kan ni kombinera NVA-aktiviteter med varandra?
Håller du dig på jakt efter Tim Wood och låt mig få veta dina
fynd…………………..
Andra relaterade artiklar:
- Lean Flow
- Kaizen
- Lean Principles
- Lean Tools
- Lean Six Sigma
- Lean Culture